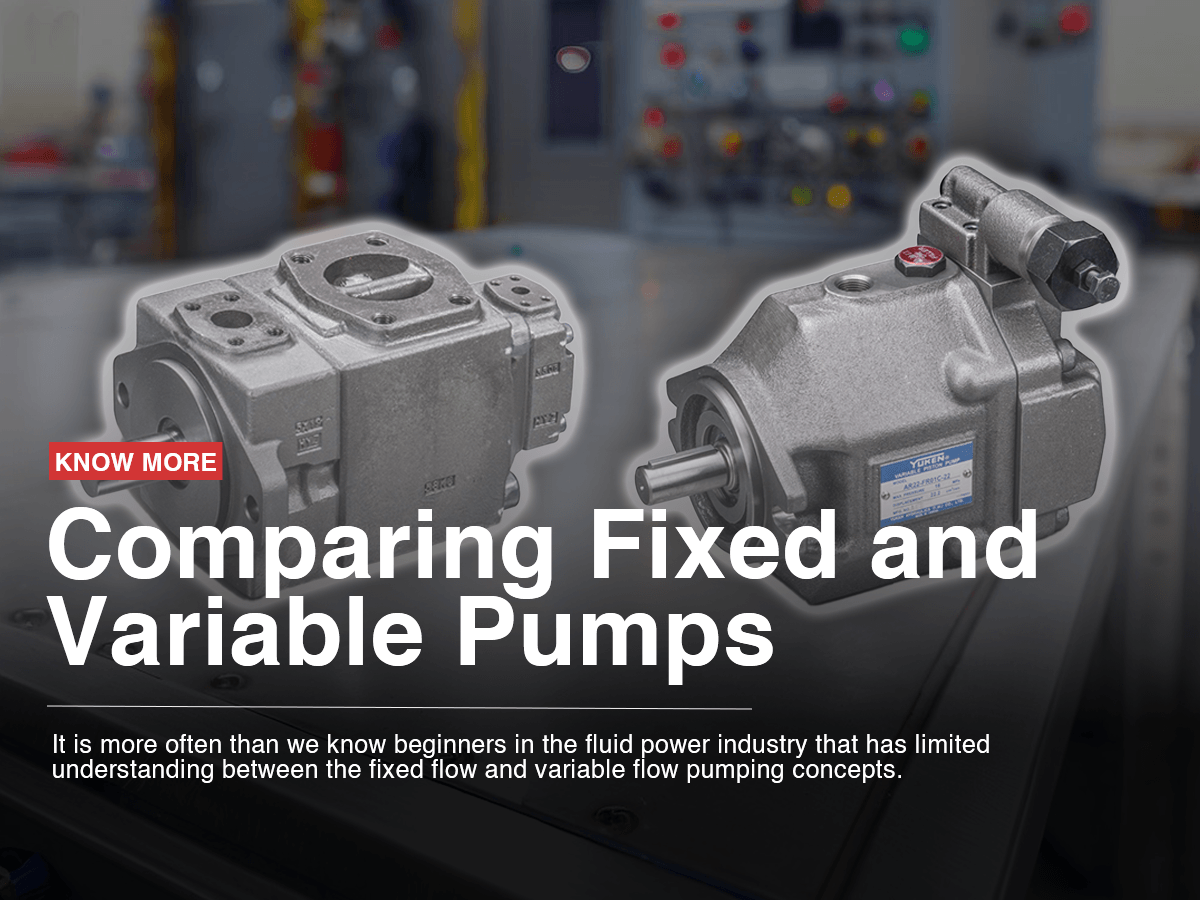
Comparing Fixed and Variable Pumps
In the fluid power industry, beginners often encounter challenges in understanding the distinctions between fixed flow and variable flow pumping concepts. An essential function of hydraulic pumps is to convert mechanical energy at their shaft into hydraulic energy capable of transferring force to downstream actuators. While both fixed and variable pumps can achieve this transfer of force, the approach to delivery varies significantly.
The displacement of a pump, determined by the gears, vanes, or pistons, defines the theoretical volume it can displace in a single revolution. For example, a 30 cc pump theoretically pushes 30 ml of fluid in one rotation. This displacement remains fixed regardless of the pump's control or downstream conditions, although actual flow may vary due to efficiency, speed, and pressure. In cases where less flow is required than the pump's rating, the excess flow must be diverted or relieved to the tank.
In contrast, a variable displacement pump offers the flexibility to adjust its displacement manually, hydraulically, or electronically. The method of displacement modification depends on the pump's structure, which varies between piston and vane pumps, and further varies within each type.
For axial piston pumps, the maximum displacement is determined by the quantity and bore area of the pistons multiplied by the stroke length. While the stroke length may remain fixed in certain cases, such as with radial and bent-axis piston motors, variable displacement axial piston pumps utilize a swashplate to guide the pistons, enabling them to compensate while rotating around the shaft's axis. The angle of the swashplate relative to the pistons governs the length of the piston stroke. With variable pumps, the swashplate is supported by bearings or bushings.
Adjacent to the swashplate, there is a control piston and a distorted piston (with a spring). A variable displacement piston pump is designed to operate at "full displacement" whenever possible. If downstream pressure exceeds the pressure compensator setting, the control piston is forced out, reducing the swashplate angle. Consequently, the pistons travel only a fraction of their potential stroke, leading to a reduction in pump volume as displacement is determined by the piston's area. The stroke continues to decrease until the swashplate angle approaches zero, at which point it pumps only enough to maintain lubrication when downstream pressure remains higher than the compensator setting.
The swashplate angle can be mechanically adjusted using a lever or wheel, but in modern applications, electro-proportional valves are employed to run the control piston, precisely adjusting pump flow as needed. This contemporary concept is commonly used in closed-loop electronic control applications, where a proportional pressure valve modifies the pump's control piston with assistance from the PLC, providing the exact flow required by the machine under varying conditions.
The operation of a piston pump differs from that of a variable-displacement pressure-compensated vane pump. In a vane pump, the rotating group is exposed to suction and pressure chambers within the housing, with vanes moving outward and inward inside the offset cam ring. A control piston is also present in variable vane pumps, exerting pressure against the cam ring. When downstream pressure rises, the control piston pushes the cam ring toward the center of the housing, reducing the difference in alignment between the cam ring and the rotating group. This effectively diminishes the pump's displacement, limiting flow to reduce downstream pressure.