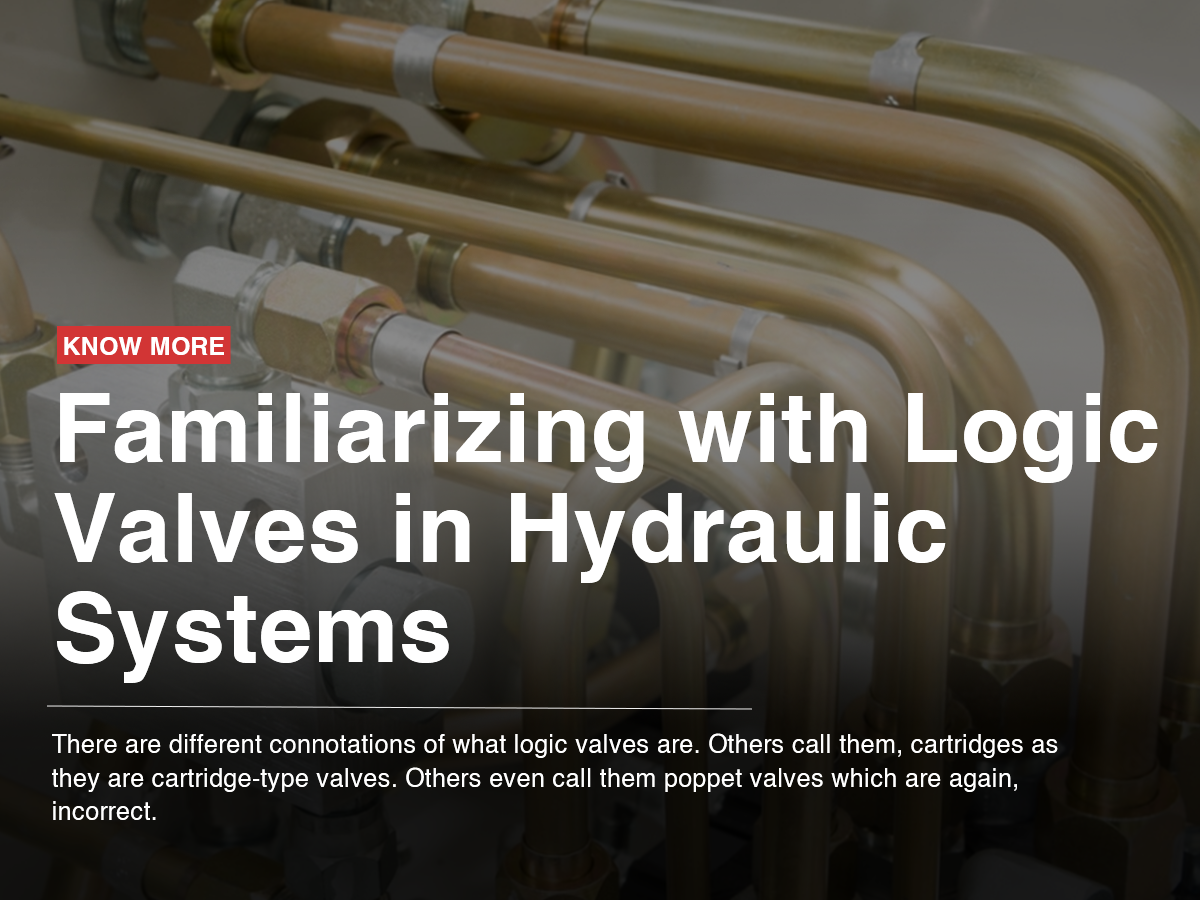
Familiarizing with Logic Valves in Hydraulic Systems
The terminology surrounding logic valves can be confusing, with some referring to them as cartridges or poppet valves, although the latter is not entirely accurate. The more appropriate term for these valves is "logic" valves, given their full-beveled seat design that prevents bypassing. Unlike the generic terms "cartridge" or "poppet," which do not distinguish them from other valve types, "logic" accurately describes their unique functionality. This article explores the purpose and advantages of logic valves as hydraulic systems continue to evolve.
One of the primary advantages of logic valves is their integration into manifolds. This feature offers several benefits, including better handling of high pressures compared to conventional hydraulic plumbing. Consequently, the use of smaller actuators is possible, leading to increased system efficiency by directing more energy towards the actual product and minimizing waste on mechanical machine operations. Additionally, logic valves reduce the need for extensive plumbing, resulting in lower installation costs. The ability to assemble manifolds before shipment saves space in plants and minimizes the occurrence of leaks. Furthermore, the elimination of hydraulic lines reduces the risk of leakage.
While the advantages of mounting valves in a manifold are clear, troubleshooting can become complex. It is crucial to understand how to read and use a hydraulic schematic as a troubleshooting tool.
The design of logic valves can vary from simple to complex, capable of mimicking almost any type of hydraulic valve. They can function as directional controls, pressure controls, check valves, and flow controls, depending on specific configurations. The operation of a logic valve hinges on its surface areas, with the force determined by the product of pressure and area.
Careful attention to installation torque settings is vital for logic valves, as they are manufactured to precise tolerances. Improper torque application, often secured by Allen bolts, can lead to malfunctioning.
The most common failure mode for logic valves is contamination, which can result from component wear, fluid overheating, or the introduction of particles to the manifold. Proper flushing of the manifold when replacing a logic valve helps prevent contaminant propagation through the system.
In conclusion, logic valves offer unique advantages when integrated into manifolds, providing efficient pressure handling and cost-effective installations. Understanding their various applications and proper maintenance practices is essential to ensure optimal performance and reliability in hydraulic systems.