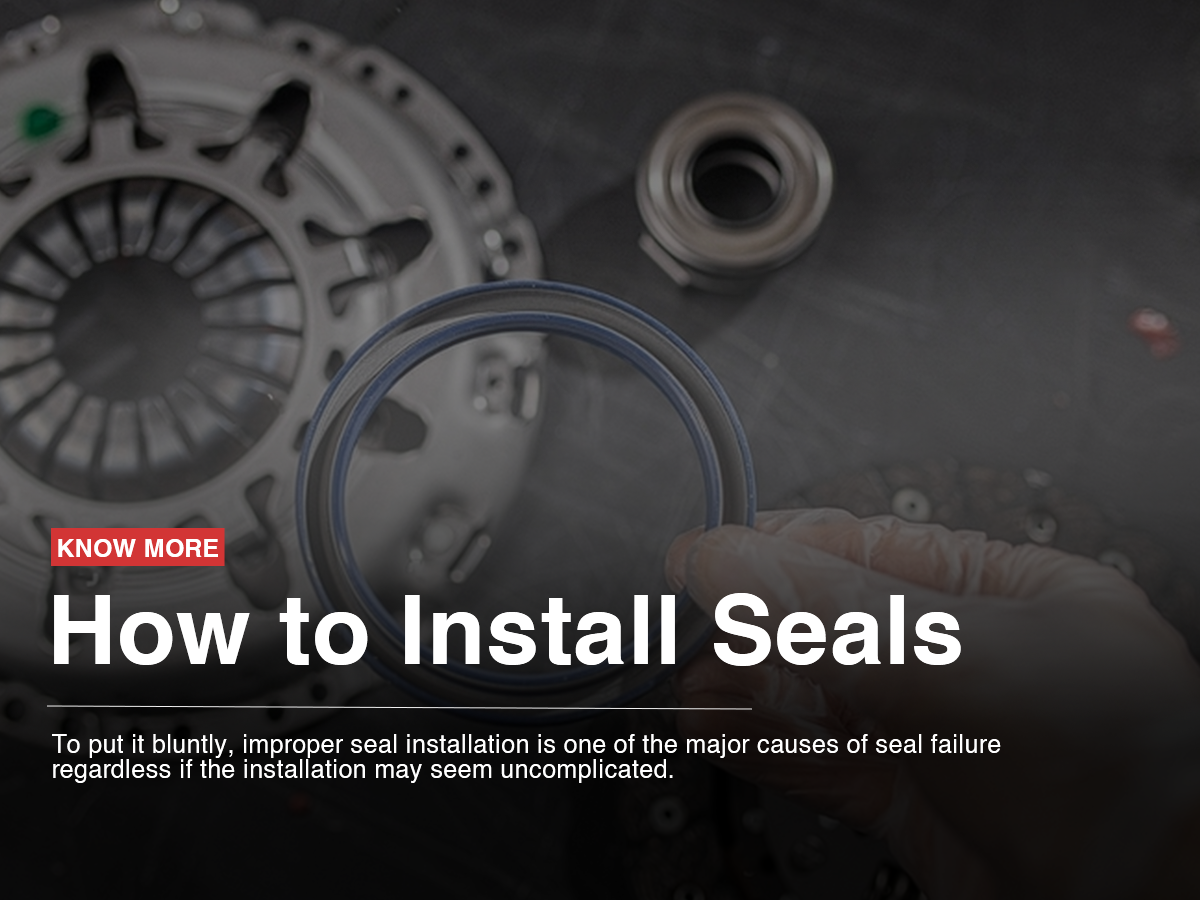
How to Install Seals?
Dirt tolerance is relatively good. Piston Pumps Axial-piston pump varies displacement by changing the angle of the swashplate. A piston pump is a rotary unit that utilizes the principle of the reciprocating pump to produce fluid flow. These pumps have many piston-cylinder combinations instead of using a single-piston. Part of the pump mechanism rotates about a drive shaft to generate the reciprocating motions, which draw fluid into each cylinder and then expel it, producing flow. There are two basic types, axial and radial piston; both are available as fixed and variable displacement pumps. The second variety often is capable of variable reversible (over center) displacement. Most axial and radial piston pumps lend themselves to variable as well as fixed displacement designs. Variable displacement pumps tend to be somewhat larger and heavier, because they have added internal controls, such as a handwheel, electric motor, hydraulic cylinder, servo, and mechanical stem. Axial-piston pumps — These are pistons in an axial piston pump that reciprocate parallel to the centerline of the drive shaft of the piston block. That is, rotary shaft motion is converted into axial reciprocating motion. Most axial piston pumps are multi-piston and use check valves or port plates to direct liquid flow from the inlet to discharge. Radial Piston Pump Inline piston pumps — The most straightforward type of axial piston pump is the swashplate design in which a cylinder block is turned by the drive shaft. Pistons fitted to bores in the cylinder block are connected through piston shoes and a retracting ring so that the shoes bear against an angled swash plate.
As the block turns, the piston shoes follow the swashplate, causing the pistons to reciprocate. The ports are arranged in the valve plate so that the pistons pass the inlet as they are pulled out and the outlet as they are forced back in. In these pumps, displacement is determined by the size and number of pistons as well as their stroke length, which varies with the swashplate angle. In variable-displacement models of the inline pump, the swashplate swings in a movable yoke. Pivoting the yoke on a pintle changes the swashplate angle to increase or decrease the piston stroke. The yoke can be positioned with a variety of controls, i.e., manual, servo, compensator, hand wheel, etc. Pressure-flow curve of fixed-displacement hydraulic pump Bent-axis pumps — This pump comprises a drive shaft that rotates the pistons, a cylinder block, and a stationary valving surface facing the cylinder block bores which ports the inlet and outlet flow. The drive shaft axis is angular in relation to the cylinder block axis. Rotation of the drive shaft causes rotation of the pistons and the cylinder block. The distance between any one of the pistons and the valving surface continually changes during rotation because the plane of rotation of the pistons is at an angle to the valving surface plane,. Each individual piston moves away from the valving surface during one-half of the shaft revolution and toward the valving surface during the other half. The valving surface is so ported that its inlet passage is open to the cylinder bores in that part of the revolution where the pistons move away. Its outlet passage is open to the cylinder bores in the part of the revolution where the pistons move toward the valving surface. Therefore, during pump rotation, the pistons draw liquid into their respective cylinder bores through the inlet chamber and force it out through the outlet chamber. Bent axis pumps come in fixed and variable displacement configurations, but cannot be reversed. Pressure flow curve of the variable-displacement hydraulic pump with ideal flow and pressure compensation In radial-piston pumps, the pistons are arranged radially in a cylinder block; they move perpendicularly to the shaft centerline. Two basic types are available: one uses cylindrically shaped pistons, the other ball pistons. They may also be classified according to the porting arrangement: check valve or pintle valve. They are available in fixed and variable displacement and variable reversible (over-center) displacement. In a pintle-ported radial piston pump, the cylinder block rotates on a stationary pintle and inside a circular reacting ring or rotor. As the block rotates, centrifugal force, charging pressure, or some form of mechanical action causes the pistons to follow the inner surface of the ring, which is offset from the centerline of the cylinder block. As the pistons reciprocate in their bores, porting in the pintle permits them to take in fluid as they move outward and discharge it as they move in. The size and number of pistons and the length of their stroke determine pump displacement. Displacement can be different by moving the reaction ring to increase or decrease piston travel, varying eccentricity. Several controls are available for this purpose. Schematic of typical proportional pump pressure compensator control Plunger pumps are identical to rotary piston types, in that pumping is the result of pistons reciprocating in cylinder bores. However, the cylinders are fixed in these pumps; they do not rotate around the drive shaft. Pistons may be reciprocated by a crankshaft, by eccentrics on a shaft, or by a wobble plate. When eccentrics are used, return stroke is by springs. Because valving cannot be supplied by covering and uncovering ports as rotation occurs, inlet and outlet check valves may be used in these pumps. Because of their construction, these pumps provide two features other pumps do not have: one has a more positive sealing between the inlet and outlet, permitting higher pressures without excessive leakage of slip. The other is that in many pumps, lubrication of moving parts other than the piston and cylindrical bore may be independent of the liquid being pumped.
Therefore, liquids with poor lubricating properties can be pumped. Volumetric and overall efficiencies are close to those of axial and radial piston pumps. Computing for pump performance The volume of fluid pumped per revolution is being computed from the geometry of the oil-carrying chambers. A pump never quite delivers the calculated, or theoretical, amount of fluid. How close it comes is called volumetric efficiency. Volumetric efficiency is found by comparing the calculated delivery with the actual delivery. Volumetric efficiency varies with speed, pressure, and the construction of the pump. A pump's mechanical efficiency is also not flawless, because some of the input energy is wasted in friction. The overall efficiency of a hydraulic pump is the product of its volumetric and mechanical efficiencies. Pumps are generally graded by their maximum operating pressure capability and their output, in gpm or lpm, at a given drive speed, in rpm. Matching pump power with the load Schematic of pump two-stage compensator control Pressure-flow curve of variable-displacement hydraulic pump equipped with pressure compensation Pressure compensation and load sensing are terms usually used to describe pump features that improve the efficiency of pump operation. Sometimes these terms are used interchangeably, a misconception that is cleared up once you understand the differences in how the two enhancements operate. To check these differences, consider a simple circuit using a fixed-displacement pump running at a constant speed. This circuit is efficient only when the load demands maximum power because the pump puts out full pressure and flow regardless of load demand.
A relief valve prevents excessive pressure buildup by routing high-pressure fluid to the tank when the system reaches the relief setting. As Figure 10 shows, power is wasted whenever the load requires less than full flow or full pressure. The unused fluid energy produced by the pump becomes heat that must be dissipated. Overall system efficiency maybe 25% or lower. Variable displacement pumps, supplied with displacement controls, can save most of this wasted hydraulic horsepower when moving a single load. Control variations include handwheel, lever, cylinder, stem servo, and electrohydraulic servo controls. Examples of displacement control applications are the lever-controlled hydrostatic transmissions used to propel windrowers, skid-steer loaders, and road rollers. These controls have no inherent pressure or power-limiting capabilities while matching the exact flow and pressure needs of a single load. And so, other provisions must be made to limit maximum system pressure, and the prime mover still must have corner horsepower capability. Moreover, when a pump supplies a circuit with multiple loads, the flow and pressure-matching characteristics are compromised. A design approach to the system in which one pump powers multiple loads is utilizing a pump equipped with a proportional pressure compensator. A yoke spring biases the pump swashplate toward full displacement. When load pressure exceeds the compensator setting, pressure force acts on the compensator spool to overcome the force exerted by the spring. The spool then transfers toward the compensator-spring chamber, ports pump output fluid to the stroking piston, and decreases pump displacement. The compensator spool returns to neutral when pump pressure matches the compensator spring setting. If a load blocks the actuators, the pump flow drops to zero. Using a variable-displacement, pressure-compensated pump and not a fixed-displacement pump minimizes circuit horsepower requirements dramatically. The output flow of this type of pump varies according to predetermined discharge pressure as sensed by an orifice in the pump's compensator. Because the compensator itself operates from pressurized fluid, the discharge pressure must be set higher - say, 200 psi higher - than the maximum load-pressure setting. So if the load-pressure setting of a pressure-compensated pump is 1,100 psi, the pump will increase or decrease its displacement (and output flow) based on a 1,300-psi discharge pressure.
A two-stage pressure-compensator control uses pilot flow at load pressure all over an orifice in the main stage compensator spool to create a pressure drop of 300 psi. This pressure drop creates a force on the spool which is opposed by the main spool spring. Pilot fluid flows to the tank through a small relief valve. A spring chamber pressure of 4,700 psi provides a compensator control setting of 5,000 psi. An increase in pressure over the compensator setting shifts the main stage spool to the right, porting pump output fluid to the stroking piston, which overcomes bias piston force and reduces pump displacement to match load requirements. The earlier stated misapprehension started from an observation that output pressure from a pressure-compensated pump can fall below the compensator setting while an actuator is moving. This does not happen because the pump is sensing the load, it happens because the pump is undersized for the application. Pressure drops because the pump cannot generate enough flow to keep up with the load. When properly sized, a pressure-compensated pump should always force enough fluid through the compensator orifice to operate the compensator. Superior dynamically Schematic of proportional pump compensator that provides the load-sensing capability Typical performance of a single- and two-stage pressure compensation A two-stage compensator is similar to the proportional compensator control with respect to its matching function. The dynamic performance of the two-stage control is better, however. This becomes obvious when one analyzes a transient that involves a sudden decrease in load flow demand, starting from a full stroke at low pressure. The single-stage control spool ports pressure fluid to the stroke piston only when pump discharge pressure hits the compensator setting. The main-stage spool of the two-stage control starts moving as soon as pump discharge pressure minus spring chamber pressure exceeds the 300-psi spring setting. Because pilot fluid flows through the orifice and because of the flow needed to compress the fluid in the spring chamber, the spring chamber pressure lags pump discharge pressure. This causes the spool to become unbalanced and shift to the right. Pump destroying happens before pump discharge pressure hits the compensator setting. Note that in a system equipped with an accumulator, a two-stage compensator control provides little advantage. In excavator hydraulic systems, however, the superiority of the two-stage compensator is evident: it provides system components with much greater protection against pressure transients. Schematic of pump control that provides a load sensing and pressure limiting Pressure-flow curve of the pump with load-sensing control.
Load sensing: the next action An identical control, which has recently become famous, is the load sensing control, sometimes called a power matching control. The single-stage valve is almost similar to the single-stage compensator control, except that the spring chamber is connected downstream of a variable orifice rather than directly to tank. The load-sensing compensator spool achieves equilibrium when the pressure drop across the variable orifice matches the 300-psi spring setting. Any of three basic load-sensing signals power a load-sensing pump: unloaded, working, and relieving. The lack of load pressure causes the pump to produce zero discharge flow at bias or unload pressure in the unloaded mode. When working, load pressure causes the pump to generate discharge flow in relation to a set pressure drop, or bias pressure. When the system reaches maximum pressure, the pump maintains this pressure by adjusting its discharge flow. Similar to the pressure-compensated pump, a load-sensing pump has a pressure-compensation control, but the control is altered to receive two pressure signals, not just one. As with pressure compensation, the load-sensing control receives a signal representing discharge pressure, but it also receives a second signal representing load pressure. This signal originates from a second orifice downstream from the first. This second orifice may be a flow-control valve immediately beyond the pump outlet, the spool opening of a directional control valve, or it may be a restriction in a fluid conductor. Comparison of these two pressure signals in the modified compensator section permits the pump to sense both load and flow. This minimizes power losses even further. The output flow of the pump varies in relation to the differential pressure of the two orifices. Just as the pressure-compensated pump increased its discharge pressure by the amount required to run the pressure compensator, the load- and flow-sensing pump's discharge pressure typically is between 200 and 250 psi higher than actual load pressure. Moreover, a load-sensing pump can follow the load and flow requirements of a single circuit function or multiple simultaneous functions, relating horsepower to maximum load pressure. This consumes the lowest possible horsepower and generates the least heat. Operator control The system can operate in a load-matched mode at the direction of an operator if the variable orifice is a manually operated flow control valve. As he opens the flow control valve, flow increases proportionally (constant pressure drop across an increasing-diameter orifice), at a pressure slightly ahead load pressure. Wasted power is very minimal with a load-sensing variable volume pump compensator. A relief valve or other means of limiting pressure must be provided since the control senses pressure drop and not absolute pressure. This problem is being resolved by a load-sensing/pressure-limiting control. This control functions as the load-sensing control previously described, until load pressure reach the pressure limiter setting. At that point, the limiter portion of the compensator overrides the load-sensing control to destroke the pump. Again, the prime mover must have corner horsepower capability. Load-sensing gear pumps Load-sensing gear pumps with two different types of hydrostats installed. The spring adjustment permits tuning pressure drop for different manufacturers' valves or line lengths Piston and vane pumps depend on their variable-displacement capability to finish load sensing. How, then, can a gear pump accomplish load sensing if its displacement is fixed? Like standard gear pumps, load-sensing gear pumps have low initial costs when compared to other designs with the equivalent flow and pressure capabilities. Nevertheless, load-sensing gear pumps offer the versatility of variable-displacement axial-piston and vane pumps but without the high complexity and high cost of variable-displacement mechanisms. A load-sensing gear pump can: give the high efficiency of load sensing without the high cost associated with piston or vane pumps, create zero to full output flow in less than 40 milliseconds with little or no pressure spiking and without pump inlet supercharging, manage circuits with low (approaching atmospheric) unload relief pressures, give priority flow and secondary flow with a low unload pressure to reduce standby and secondary loaded power draw, and the interchange with load-sensing vane or piston pumps without having to alter the line of component sizes. Combined control is accomplished by incorporating a pilot relief, which causes the hydrostat to act as the main stage of a pilot-operated relief valve Unloader control has been added to the load-sensing gear pump. The control uses a poppet or a plunger to permit maximum flow at the minimum pressure drop across the unloader with minimal control movement Load-sensing piston pumps utilize a pressure compensator and a hydrostat to vary volumetric output to a system in reference to load pressure and flow requirements. A hydrostat is a spring-loaded device that meters flow according to the spring force across its equal but opposing effective areas.
It may be restrictive, as in a series circuit, or it may bypass primary load pressure to a secondary or tank pressure. To simply explain, a hydrostat separates the total flow into two flows: one represents the required flow and the other represents the required pressure of the primary circuit. A load-sensing piston pump uses its hydrostat to manage output flow relative to load pressure and bypasses the excess pump flow to a secondary route, which may be ported to the tank or to a secondary circuit. On the other hand, a load-sensing gear pump uses a hydrostat in combination with an unloader to vary its volumetric output in response to load and flow requirements. Because load-sensing piston and gear pumps both use a single load-sensing signal to control pump discharge pressure and flow, they are interchangeable in load-sensing circuits. Both types have much in common and offer substantial power savings over systems using fixed-displacement pumps. Both offers reduced power consumption in the running mode - when flow and pressure are required to operate a function. They also preserve power in the standby mode - when the system is idling or in a non-operational mode. Furthermore, they can minimize the required size - and, therefore, cost- of valves, conductors, and filters needed for the circuit. The load-sensing gear pump reduces power consumption in the running mode by isolating total discharge flow according to a remote primary function pressure and a primary flow. This is accomplished through a single load-sensing signal originating from the priority circuit and routed as close as possible to the discharge side of the pump's gears. Connecting an unloader control to the pump circuit permits the system to conserve power in the standby mode of operation as well as in the running mode. This control must be installed in parallel with the inlet port of the hydrostat and as close as possible to the discharge side of the gears. It must be piloted by the same load-sensing signal that causes the pump to dump all flow from the outlet to the secondary circuit and at a pressure well below the hydrostat's pressure-drop setting in the standby mode. The unloader control must run off the same remote load-sensing signal that controls the hydrostat. Unlike the hydrostat, the unloader poppet of the unloader control is designed with opposing areas having a ratio of at least 2:1. Any line pressure sensed that exceeds 50% of pump discharge pressure will close the unloader control. The capability of the unloader control to unload the pump to near atmospheric discharge pressure is controlled by the poppet or plunger spring force. The unloader control is set to the lowest value to maintain the internal pressure loading of the gear pump. When compared to a standard fixed-displacement gear pump circuit, this control can reduce standby power consumption by 90%. Dual and combined controls This cutaway shows combined control, which has an adjustable hydrostat contained within the unloader control. Locating the hydrostat within the low-unload control allows all piston areas to operate from a single load-response signal. It is intended for applications using large pumps where secondary flow bypasses the tank.
The load-sensing signal can be conditioned by restricting pressure in the remote sensing line or taking it to 0 psig. Doing so causes the hydrostat and the unloader control of the load-sensing gear pump to respond to the conditioned signal according to the discharge pressure. This is completed by providing a pilot relief, which causes the hydrostat to act as the main stage of a pilot-operated relief valve. The ability to condition the load-sensing line is patented and makes the load-sensing gear pump useful for functions other than just load sensing. The combined-control load-sensing gear pump is planned for large-displacement pumps and bypasses secondary flow to the tank. This can be utilized in similar applications as the dual-control pump and this is also patented. Nonetheless, because secondary flow must be directed to the tank, it cannot be used when the secondary circuit drives a load.