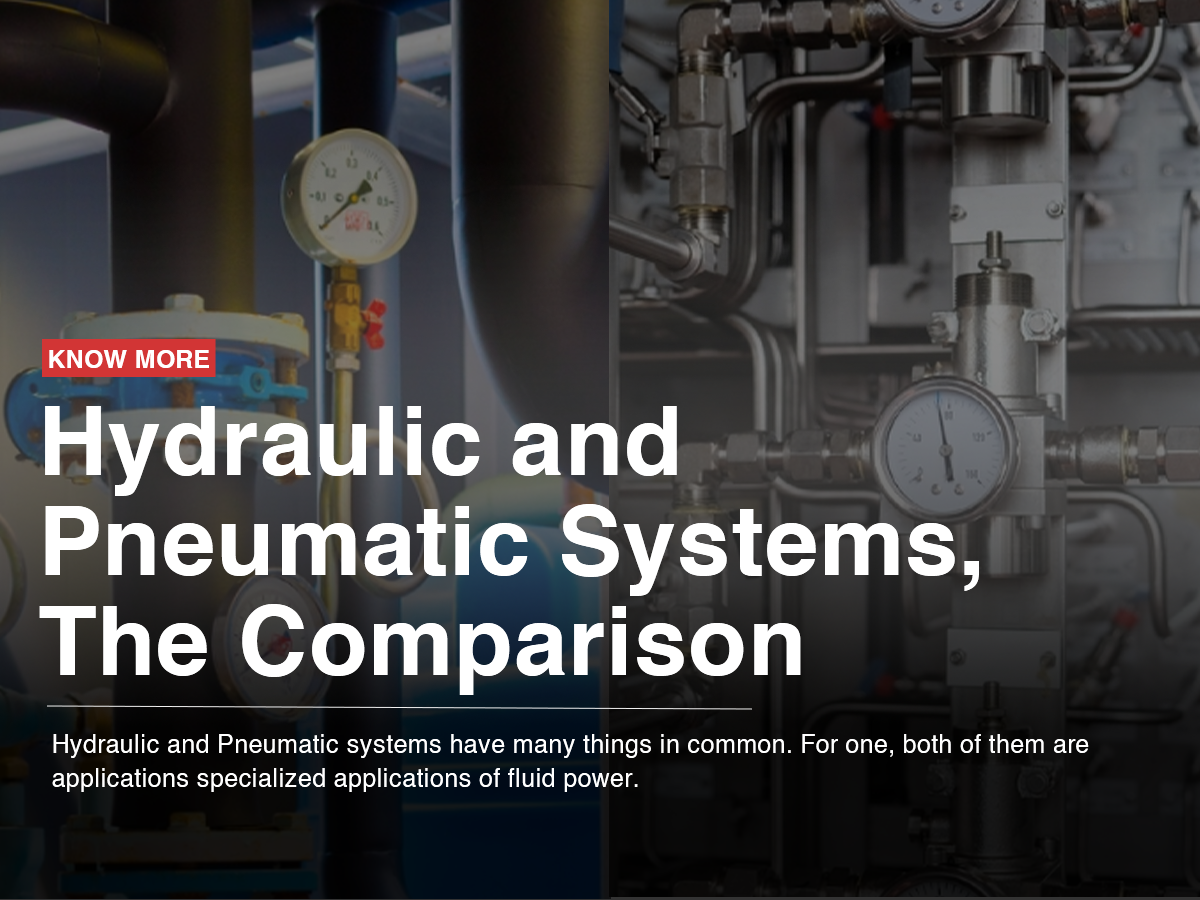
Hydraulic and Pneumatic Systems, The Comparison
Hydraulic and Pneumatic systems share common characteristics as applications of fluid power, utilizing pumps as actuators, controlled by valves, and employing fluids for mechanical energy transmission. However, there are notable differences between the two systems, each with its own set of advantages and disadvantages.
Pneumatic systems rely on compressed air or inert gases and find application in various fields such as construction, robotics, food manufacturing, and medical settings. These systems are favored for shock absorption applications due to the compressibility of gas, which helps protect equipment from shock damage.
In contrast, Hydraulics involves the use of pressurized liquids for power generation, control, and transmission. These systems are commonly used in elevators, dams, machine tools, amusement parks, and various heavy machinery applications. While they offer more significant force capabilities and versatility, hydraulics can be more complex and costly compared to pneumatic systems.
A summarized overview of the benefits and disadvantages of both systems is as follows:
Pneumatic System:
- Advantages: Lower cost, flexibility, quick conveyance of items with compressed air, ease of installation and portability, clean and dry operation, agility in system changes, and safety.
- Disadvantages: Limited potential force compared to hydraulics, higher energy costs due to heat losses during air compression, increased noise production.
Hydraulic System:
- Advantages: Capable of moving heavier loads, multifunctionality including lubrication, cooling, and power transmission.
- Disadvantages: Higher initial costs than pneumatic systems, unsuitable for food applications due to the risk of hydraulic oil leaks.
Ultimately, selecting the appropriate system depends on specific application requirements, considering factors like force needs, cost considerations, and environmental constraints.