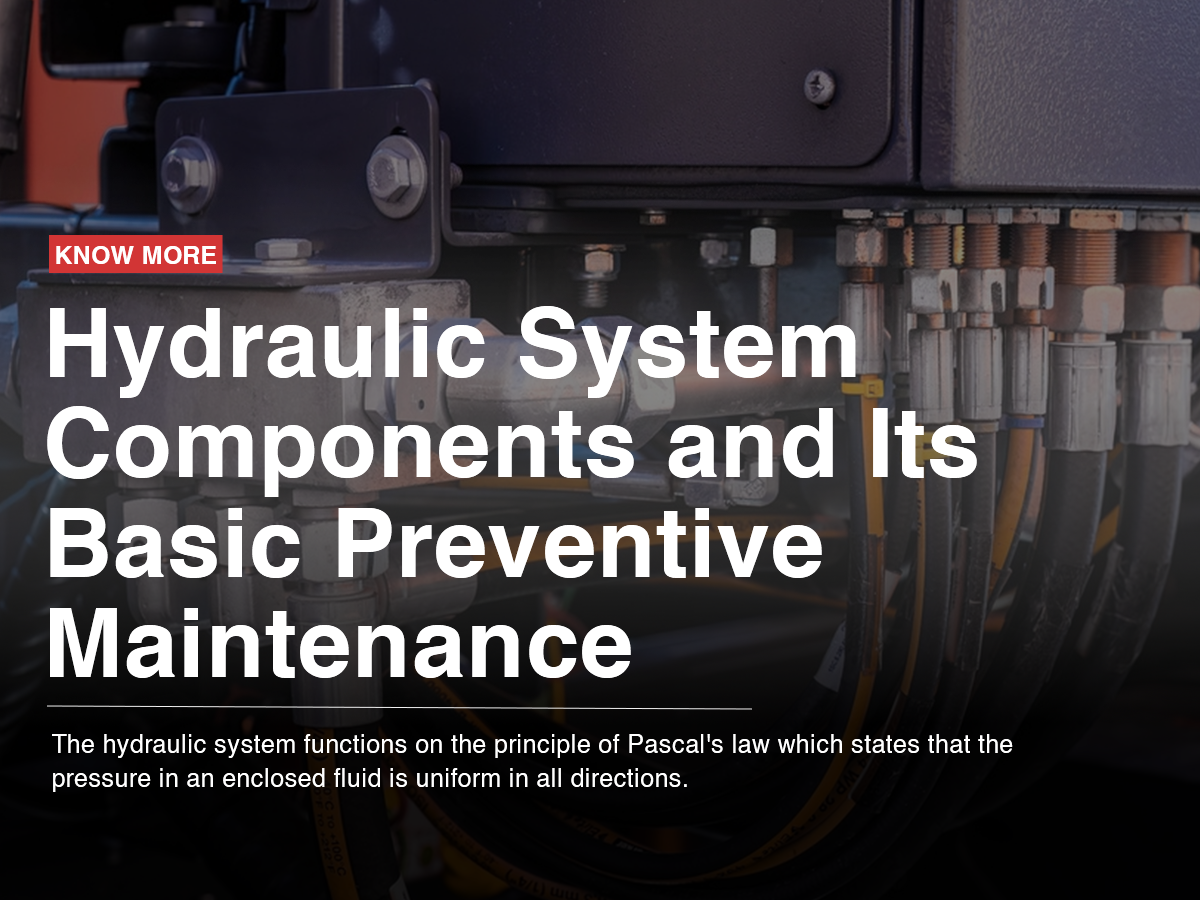
Hydraulic System Components and Its Basic Preventive Maintenance
The hydraulic system operates based on Pascal's law, which ensures uniform pressure in enclosed fluids. The term 'hydraulics' originates from the Greek word 'hydraulikos,' meaning water organ, indicating its use of fluids to perform mechanical tasks. Nowadays, hydraulic systems are widely used in machinery and equipment control. Understanding the main components of hydraulic systems and how to care for and troubleshoot them is crucial, as it represents a significant investment for industrial companies.
There are two types of hydraulic systems: the open-center system and the closed-center system. The open-center system offers smoother operation of actuating mechanisms by eliminating continuous pressurization. In contrast, the closed-center system provides immediate pressure availability once the selector valve is positioned.
The main components of a hydraulic system consist of a hydraulic pump, reservoir for hydraulic fluid, filter, actuator, accumulator, directional control valve, flow control valve, pressure relief valve, and pipes and fittings. Each component serves a specific function to ensure proper system operation.
The hydraulic pump is responsible for converting mechanical energy into hydraulic/pressure energy and delivers fluid to the hydraulic circuit. Hydraulic filters remove foreign particles from hydraulic oil, preventing contamination. The actuator converts pressure energy into mechanical force and motion, available in linear and rotary types. Accumulators store pressurized hydraulic fluid for future use and can provide a cushioning effect.
Directional control valves regulate fluid flow direction, while flow control valves control the actuator's speed by adjusting the valve opening area. Pressure relief valves play a vital role in maintaining system pressure within a specified range, protecting hydraulic components from excessive pressure.
Pipes, tubing, and flexible hoses are used to convey fluid within the hydraulic system, and fittings connect the different units of the system. Proper preventive maintenance is essential to prevent system breakdowns and keep contaminants out of the hydraulic system. Routine checks on hydraulic fluid levels, breather caps, filters, pressure gauges, and system temperature are recommended. Inspection of hydraulic hoses, fittings, proportional/servo valves, and the electric drive motor is necessary to detect leaks, frays, or overheating issues. Regular monitoring and maintenance will ensure the hydraulic system operates smoothly and efficiently.