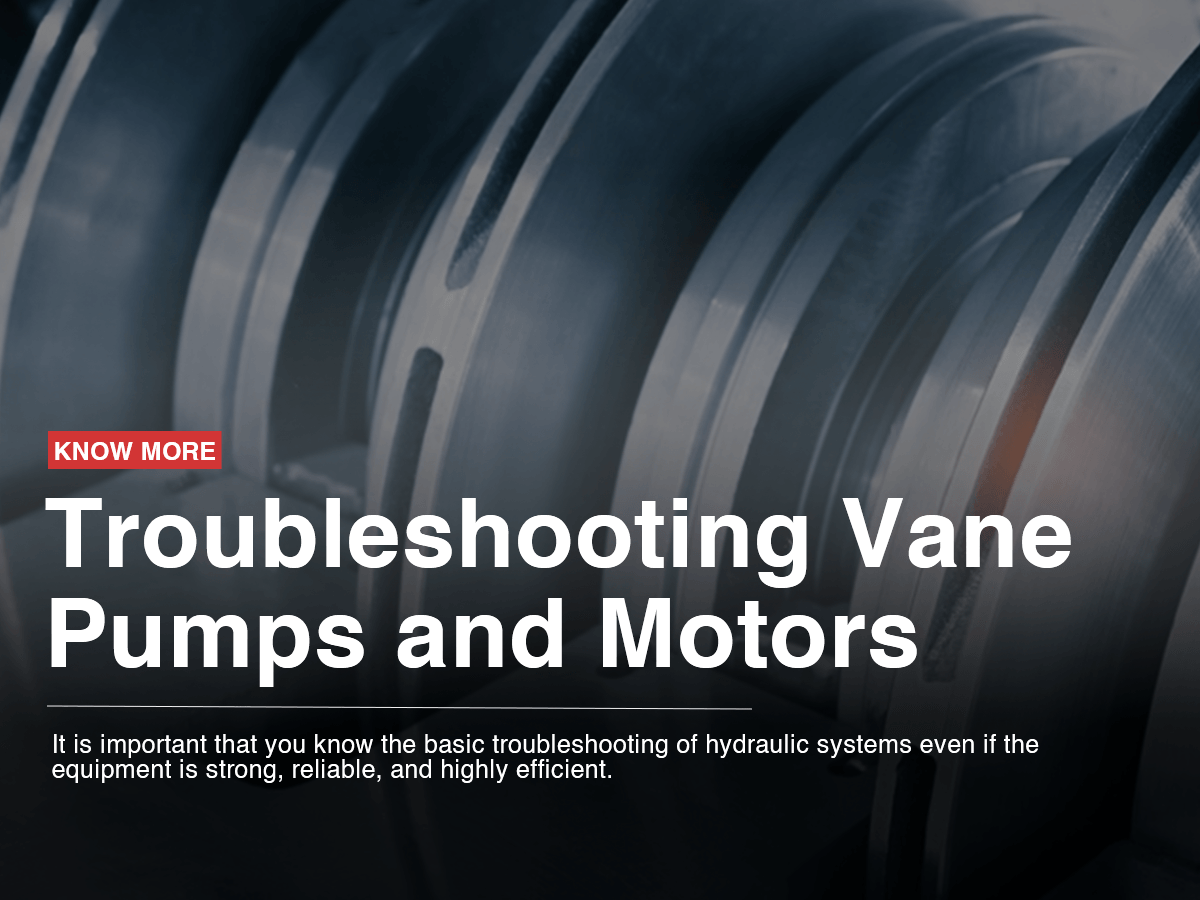
Troubleshooting Vane Pumps and Motors
Understanding the basic troubleshooting of hydraulic systems is essential, even if the equipment is robust, reliable, and highly efficient. Over time, wear and, in many cases, misuse can lead to the need for repair skills. One common cause of failure in vane pumps and motors is contaminated hydraulic fluid, accounting for more than 80% of such failures.
Thus, the primary and straightforward tip is to maintain clean fluid. A filtration plan should be established and implemented to keep the fluids clean, incorporating cleanliness targets suitable for the system and application environment, along with detailed maintenance procedures. This approach serves as the first line of defense against the failure of hydraulic components, particularly vane-type pumps and motors.
It is important to recognize that fluid cleanliness should be a critical consideration in the system design, just like the selection of pumps, valves, actuators, and bearings. Simply choosing a filter from a manufacturer's catalog may not adequately address the specific requirements of the system.
To significantly reduce hydraulic system failures related to contaminated fluids, proper selection and placement of contamination-control devices should be pursued. This cost-effective approach ensures that the investment in filters and elements is quickly recovered through improved performance, increased component life, extended oil life, enhanced uptime, and fewer repairs.
Identifying the sources of contamination is crucial in troubleshooting dirty fluids. Four primary sources of contamination are: contaminated new oil, built-in contamination during manufacturing, outside sourced contamination, and internally caused contamination.
To maintain cleanliness, it is crucial not to assume that new hydraulic fluids are clean. Even new or rebuilt machines should be run with aggressively filtered fluids to prevent potential contaminants from causing damage. Good housekeeping practices are essential, particularly in keeping environmental contaminants away from the equipment.
One significant cause of component damage unrelated to dirty fluids is cavitation, which occurs when bubbles form and implode within the fluid, causing high temperatures that can weaken and erode metal parts. Identifying and addressing the causes of cavitation are essential to prevent component damage.
Another form of damage is erosion, which occurs when high-speed oil streams propel contaminant particles against surfaces, causing abrasion. An aggressively applied filtration plan can help mitigate erosion damage.
Catastrophic failures are usually a result of various causes, such as over-pressurization, airlocks, misalignment, and improper modifications. An effective filtration plan can serve as insurance against these failures as well.
Overhauling a vane-type pump can be done in the field without special tools. The process involves disconnecting the power source, removing the cover plate bolts, and following specific steps to disassemble and reassemble the pump's components.
It is essential to use original replacement parts when rebuilding a cartridge, as using imitation or "will fit" parts may lead to premature pump failure and damage to other system components. Pump manufacturers offer rebuild kits and detailed instructions for the operation, ensuring proper maintenance and longevity of the hydraulic system.