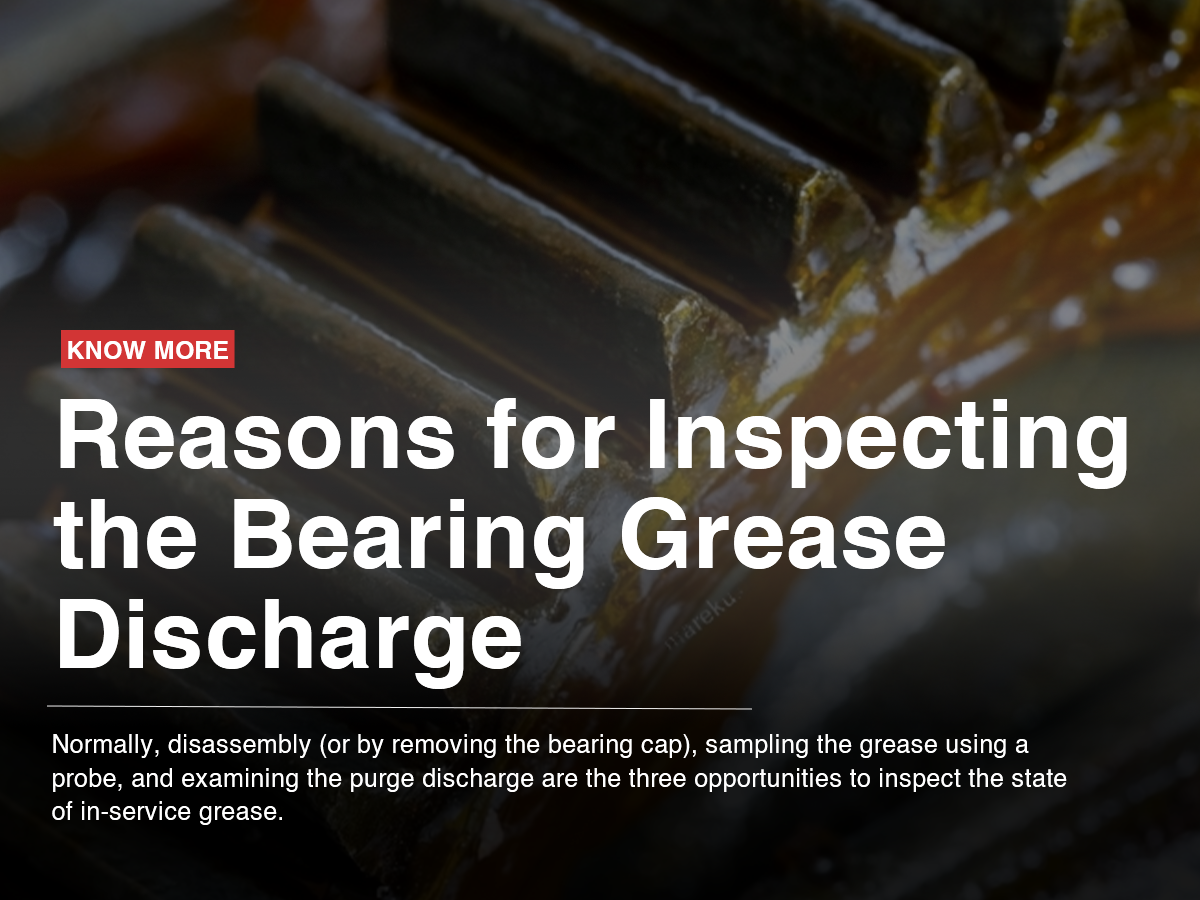
Reasons for Inspecting the Bearing Grease Discharge
In the typical examination of in-service grease, there are three opportunities to inspect its condition: disassembly (or bearing cap removal), sampling the grease using a probe, and analyzing the purge discharge. The purge discharge refers to the grease that is expelled from exhaust ports, seals, and other openings during machine operation or relubrication. Machines equipped with purge mechanisms offer distinct advantages for convenient inspections at any frequency. These systems are generally classified as "total loss" setups, as the purged grease is not recovered for reuse.
To facilitate inspection, a grease discharge trap (GDT) serves as an inspection device. This trap involves a simple barb fitting installed in the purge port, where a 1½-inch zip-lock plastic bag is attached using an O-ring. This arrangement allows the purged grease to be collected directly in the bag, enabling easy inspection, disposal, and sampling. Utilizing a GDT offers several benefits, including enhanced cleanliness, easy disposal of the collected grease, protection against contamination, and the ability to monitor the grease discharge volume and condition effortlessly.
Various machines support a purge stream, such as electric motor bearings, pillow-block bearings, blower/fan bearings, grease-lubricated gearbox bearings, mechanical couplings, process pump bearings, compressor bearings, hinge pins, journal bearings, agitator bearings, extruder bearings, and calendar roll bearings. While purging grease through a bearing is commonly practiced, it is not always recommended, as it may not be suitable for certain applications.
The importance of purge discharge lies in its ability to provide a historical account of the bearings' condition, reflecting the quality of lubrication and, consequently, the bearing's reliability. By examining the purged grease, one can detect various states of grease, such as incorrect or mixed grease, degraded grease, or contaminated grease. Understanding the grease's condition aids in identifying potential issues and helps in making informed decisions regarding lubrication practices.
Two methods of grease purging are the Fresh Grease Purge (FGP) method and the Grease Purge and Volume (GPV) method. Each method is suitable for different applications based on factors such as bearing speed, purge path availability, and environmental contamination.
Inspecting the discharge can be carried out through visual assessment, lab analysis, artist spatula/light table inspection, particle inspection, ferrous density tests, and oil content tests. Regular inspection and analysis of grease discharge should be part of the skill set of operators and technicians responsible for lubrication, maintenance, and machine reliability, as it provides valuable insights for the overall operation of the equipment.