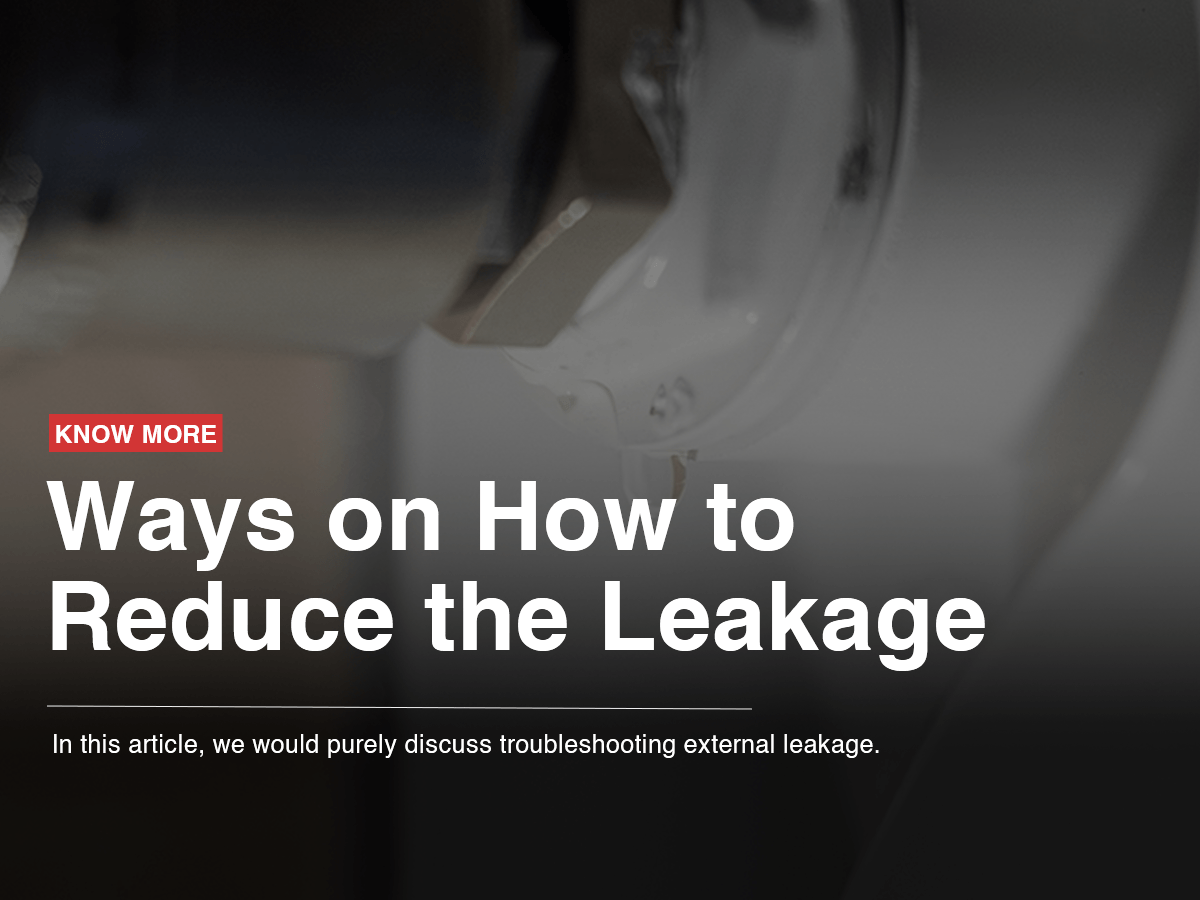
Ways on How to Reduce the Leakage
In the realm of leakage troubleshooting, this article focuses solely on external leakage, as internal leakage involves a more complex discussion. While monitoring and addressing external leakage are relatively straightforward, preventing such issues can present certain challenges. Consequently, the process of eliminating or reducing leakage should be a collaborative effort involving a company's management and maintenance department.
The predominant cause of external leakage, surpassing all other factors, is the utilization of tapered pipe threads. When components with pipe threads are assembled, they create a conical helix space that becomes a leakage path. To effectively address this issue, it is advisable to avoid using NPT (National Pipe Taper) threads altogether and instead opt for straight thread connections, which are inherently leak-free. Attempts to mechanically crush the threads or apply sealing tapes and other sealant materials often prove inadequate, particularly when connections require frequent opening and remaking.
Despite ongoing recommendations from technical and professional societies to abandon NPT plumbing, regrettably, many manufacturers still adhere to this outdated technique. However, positive changes are emerging, with larger OEMs and industries like automotive and primary metals beginning to specify the elimination of NPT plumbing in their requirements.
Companies procuring and operating hydraulic equipment must consider investing in machinery featuring straight aligned connections. Although these connections may entail slightly higher initial equipment costs, they will prove cost-effective in the long run by reducing the need for adding make-up fluid to the system and minimizing leakage issues. Conversely, companies that do not specify straight thread connections may have to accept the occurrence of leakage and bear the associated costs.
Aside from tapered threads, other potential causes of external leakage should be taken into account during troubleshooting:
- Vibration: Vibrations can loosen connections, leading to leakage issues.
- Improper Plumbing Assembly: Careful attention must be given to the correct tightening of fittings during the assembly process.
- Damaged or Worn Seals: Linear and rotary components may suffer from defective seals, which should be replaced to prevent or minimize future seal leakage.
In conclusion, proactive planning before equipment procurement is a highly effective approach to minimize the need for troubleshooting due to external leakage. By adopting best practices and investing in leak-resistant components, companies can ensure smoother hydraulic operations and reduce maintenance and operational costs in the long term.