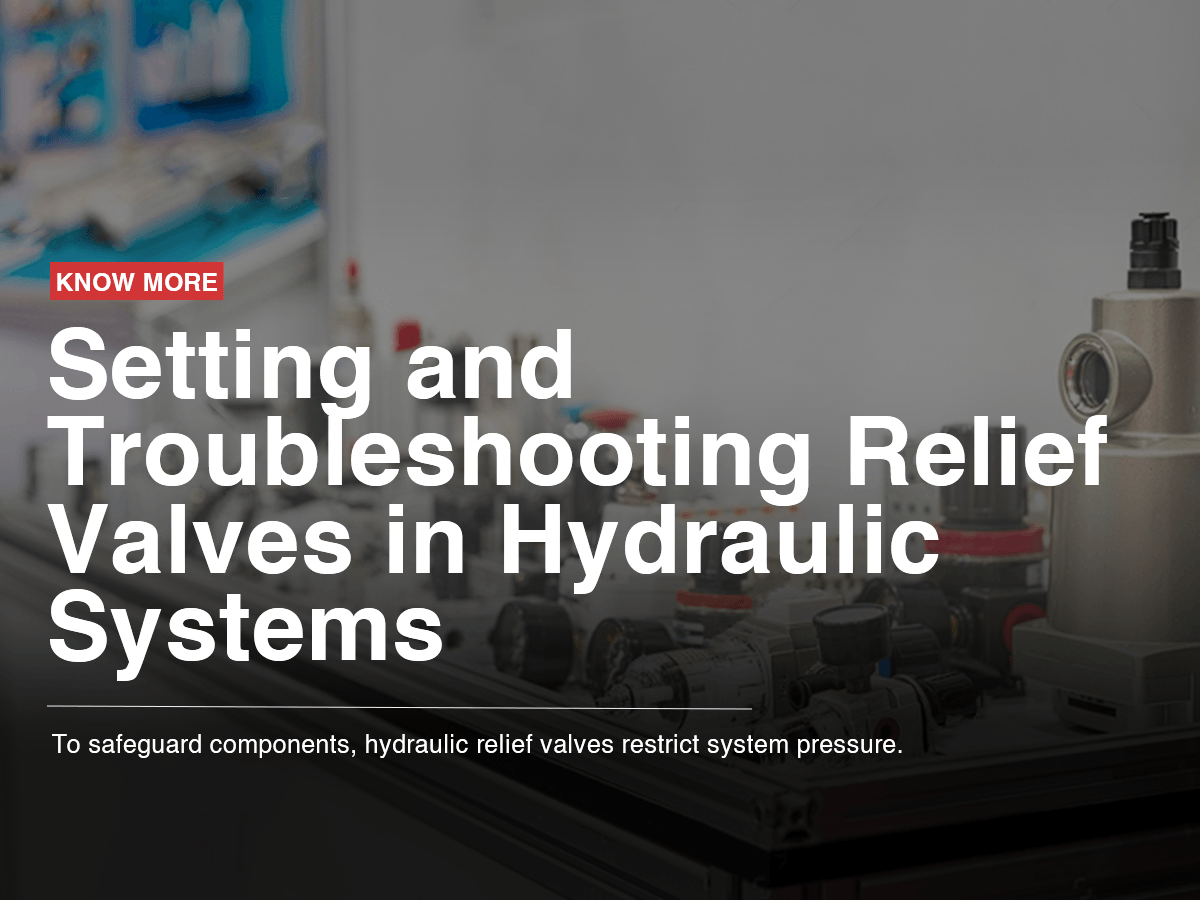
Setting and Troubleshooting Relief Valves in Hydraulic Systems
To ensure the protection of hydraulic system components, hydraulic relief valves play a critical role in restricting system pressure and limiting the system's maximum output force. These valves operate by balancing the hydraulic force with a variable spring force, releasing heat when they open in response to a predetermined pressure. Properly adjusted relief valves ensure the system functions optimally and regulates the amount of heat generated.
However, it is essential to set up relief valves correctly and monitor them consistently to prevent malfunctions that could cause harm to the hydraulic system. The following steps outline the process of setting a pressure relief valve:
Step 1: Refer to machine drawings to identify the circuit that requires adjustment and locate the circuit relief valve, typically connected to the pump in parallel and placed close to the pump.
Step 2: Disconnect the hydraulic hose from the relief valve's system side, using appropriate JIC caps or plugs to seal the hose and valve. The relief valve's return or tank side should not be capped, as this can prevent hydraulic fluid loss and system contamination.
Step 3: Attach a pressure gauge between the pump and the relief valve using an available port or an adapter if needed.
Step 4: Loosen the pressure relief valve adjustment to reduce pressure as much as possible. Start the machinery and activate the hydraulic circuit, ensuring the pressure gauge reads nearly zero.
Step 5: Gradually turn the relief valve adjustment clockwise until the gauge reading matches the specified pressure in the machine specifications, determining the valve's "cracking" pressure. Securely tighten the adjuster lock nut to maintain the desired setting.
Step 6: Verify the relief valve setting once the gauge reading corresponds to the required pressure, preventing unintentional adjustments by firmly tightening the adjuster lock nut.
Recognizing signs of pressure relief valve failure is crucial for timely maintenance and safety. Three indicators of potential valve failure include:
-
Failure to reach proper pressure: If the relief valve releases pressure before the system reaches its maximum pressure, or if it continuously leaks or chatters, there may be an issue with the valve's calibration or functionality.
-
Overpressure without valve activation: If the system is over-pressured, and the pressure relief valves have not activated, it indicates a potential valve malfunction due to contaminants or misalignment.
-
Leaking valves: Valve leaks can lead to reduced efficiency and productivity in the system, requiring thorough evaluation and maintenance to identify the cause and ensure proper functioning.
In case of a pressure relief valve failure, it is crucial to investigate the underlying cause rather than simply replacing the valve. Troubleshooting should be performed to determine the root issue for effective resolution and to maintain a safe operating facility. Properly installing, monitoring, and maintaining pressure relief valves in hydraulic systems are vital aspects of ensuring system safety and performance.