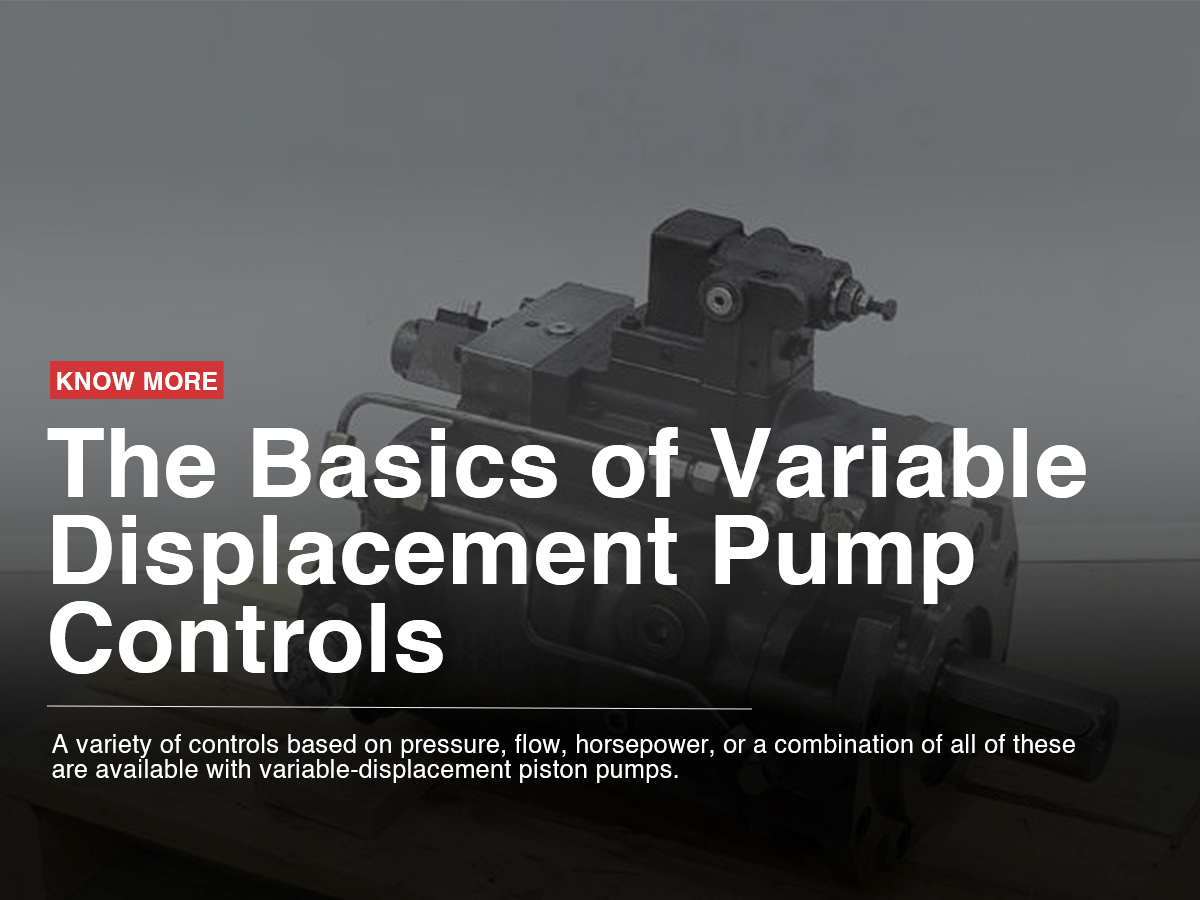
The Basics of Variable Displacement Pump Controls
Vane or gear pumps are typically straightforward to control, operating either in a loaded state or not (with all flow returning to the reservoir). The flow rate is solely determined by the input RPM since these devices are usually fixed-displacement pumps. This system is referred to as an open-loop system, with flow returning to the tank after completing the operation. On the other hand, closed-loop systems allow for more precise control possibilities.
Variable-displacement piston pumps offer various control options based on pressure, flow, horsepower, or a combination of these parameters. The pump's flow capacity is determined by a rotating set of pistons, and altering the pistons' strokes changes the pump's displacement. This can be achieved by tilting the swash plate, adjusting the rotating group's angle in a variable displacement pump.
Pressure-compensated control is a basic approach for variable-stroke piston pumps, where a strong spring and an internal piston offset the swashplate to maintain maximum displacement. When the system pressure is strong enough to overcome the spring pressure, the swash plate angle is reduced, leading to decreased pump flow and pressure. This control is simple but effective, and it suits certain applications.
Load-sense compensators, another option, use a softer spring to control the swash plate. The pump has a load-sense port that senses upstream pressure, and as the pressure demand increases, the load-sense piston is pushed back. The swash plate angle changes in response to the pressure demand until it balances the piston, and the pump increases flow accordingly. This system allows the pump to generate flow at the pressure required by the load plus the spring offset.
For even more precise control, a proportional throttle or electronic proportional flow control can be used with the load-sense system. With additional control options, you can remotely adjust the pressure compensator and set multiple system pressures as needed.
Horsepower or torque-limiting controls provide the capability for a pump to accept the maximum amount of input torque, increasing output flow and pressure at the specified setting. This allows the pump to maximize flow and pressure while not exceeding its available horsepower.
Selecting the right pump for a new application requires the expertise of a licensed hydraulic or fluid power specialist who can guide you in making the best choice.