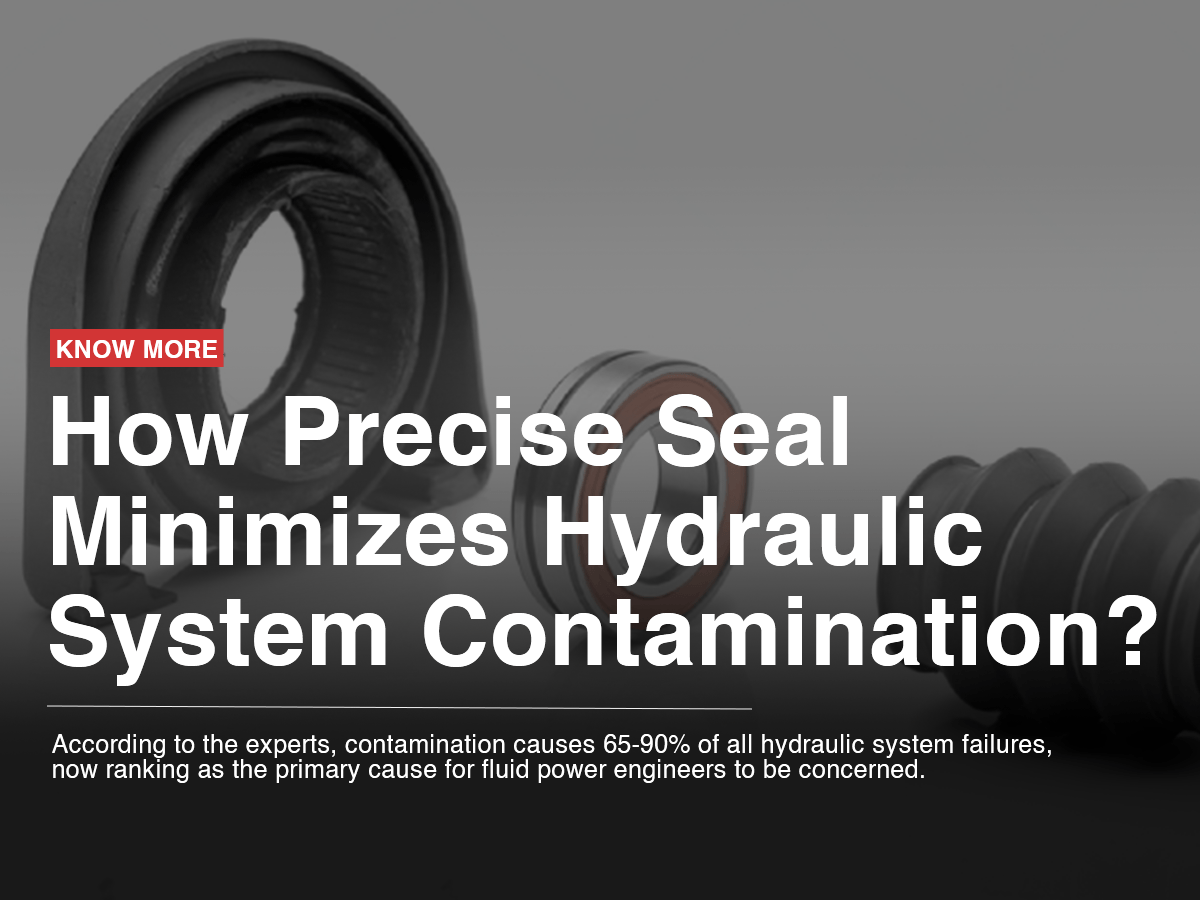
How Precise Seal Minimizes Hydraulic System Contamination?
As per expert analysis, contamination is responsible for 65-90% of all hydraulic system failures, making it a major concern for fluid power engineers. Even with advancements in filters, hydraulic oil can still become contaminated, leading to a shortened lifespan of hydraulic equipment. Contamination can occur due to particles left in the system during manufacturing, improper filtration of oil before entering the system, particles and condensing water entering through openings or bypassing seals, and wear on components that generates particles.
Component wear can result from lubricated surfaces contacting each other, clearance-sized particles damaging surfaces, adhesive wear separating material from a surface through friction welding, fatigue or point loading causing elastic damage to a component's surface, and erosion from silt-sized particles forming abrasive slurries that destroy surfaces. Regardless of the method of abrasion, internal or ingress contamination by particles can be reduced or prevented by employing appropriate seals.
Seals play a crucial role in preventing leaks and internal contamination. Through Lubrication Management, engineered seals regulate lubrication between primary and secondary seals, reducing heat generation and wear while extending component service life. Wiper seals, located on dynamic surfaces facing the external environment, prevent the ingress of contamination, while wear rings absorb transverse forces and prevent metal-to-metal contact to avoid internal contamination.
Static seals serve as a final line of defense against internal leaks and external debris entering the hydraulics and are often placed near threaded components. Proper selection of seal materials is essential, considering chemical compatibility with hydraulic fluid and operating temperatures. Expert seal suppliers can offer guidance on material storage and shelf-life limits.
Proper installation methods should be followed to avoid seal damage. Engineers should ensure a clean and well-lit assembly area, eliminate machining residues, deburr and chamfer sharp edges, cover screw thread tips, use installation tools without sharp edges, and ensure correct lead-in chamfers for cylinder bores and rods.
To optimize hydraulic systems' performance and lifespan, engineers must address potential contamination and wear issues by selecting appropriate seals, considering the four causes of contamination, chemical compatibility, temperature, system pressure, and proper storage and installation practices. By implementing these measures, expensive hydraulic failures can be prevented, and the longevity of the system can be extended.