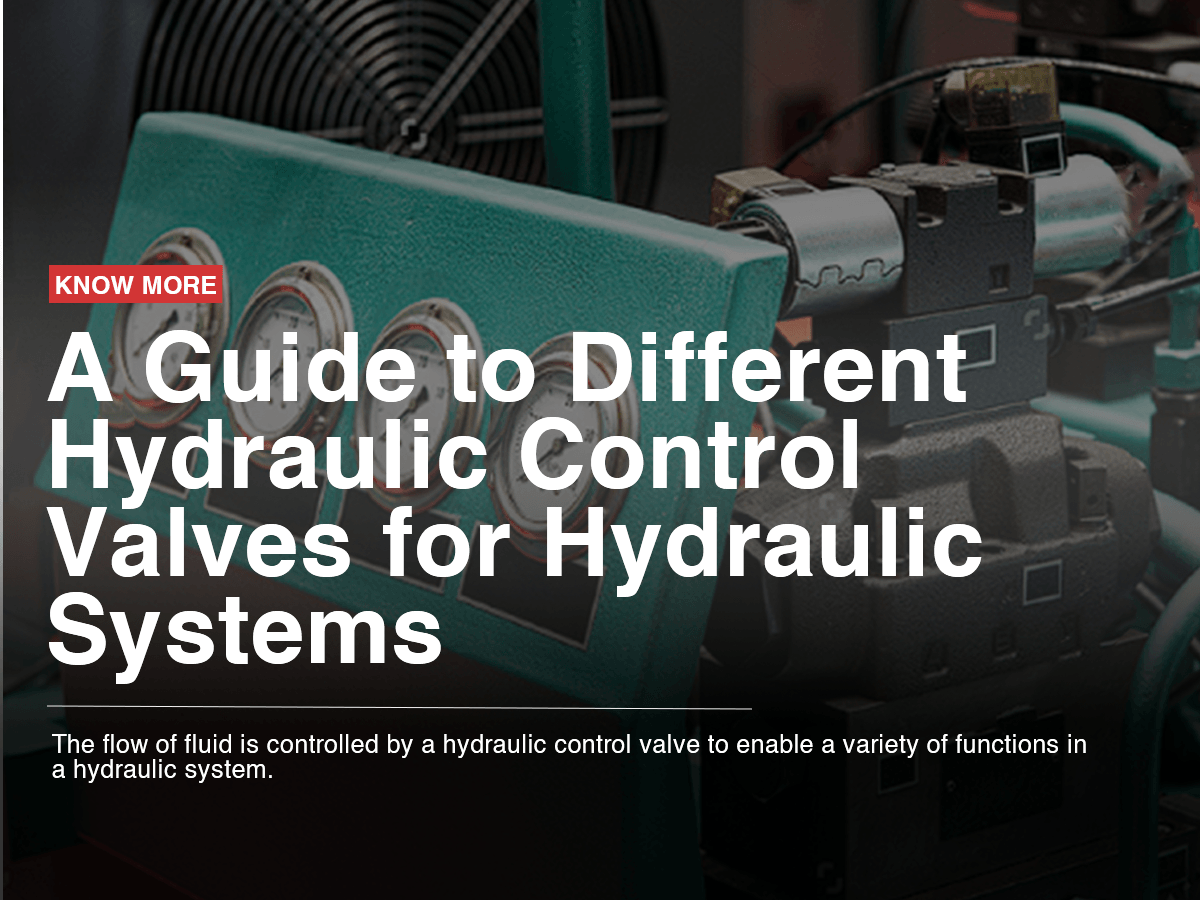
A Guide to Different Hydraulic Control Valves for Hydraulic Systems
Hydraulic control valves play a crucial role in regulating fluid flow within hydraulic systems, enabling various functions such as controlling the speed of motors, actuators, or cylinders. These valves are essential for maintaining the smooth operation and performance of hydraulic equipment. They can also depressurize specific sections of a hydraulic circuit, facilitating maintenance tasks like hose fittings replacement.
To ensure proper performance, control valves need to be selected based on flow rate requirements, which can be measured in mass flow rate, weight flow rate, or volumetric flow rate. Different types of valves serve various purposes, with directional control valves responsible for starting, stopping, and changing fluid flow. Pressure control valves, on the other hand, manage excess pressure in hydraulic systems, serving functions like unloading, counterbalancing, and relief.
Flow control valves are designed to modify actuator speed by controlling the flow rate, allowing for smooth control of fluids and gases. Various models of flow control valves, including fixed flow, adjustable flow, throttling flow, and pressure-compensated flow control, cater to different applications across industries.
Several types of hydraulic control valves are available to support diverse equipment and applications, such as ball, butterfly, diaphragm, gate, globe, pinch, needle, and plug valves. Each type has unique features and advantages, making them suitable for specific scenarios.
When choosing the correct hydraulic control valve, factors like valve arrangement, media type, port size/type, operating voltage, flow rate, operating pressure, and temperature range should be considered. Proper selection is essential to ensure optimal performance and efficiency in various applications, ranging from industrial automation to food processing and aerospace industries.