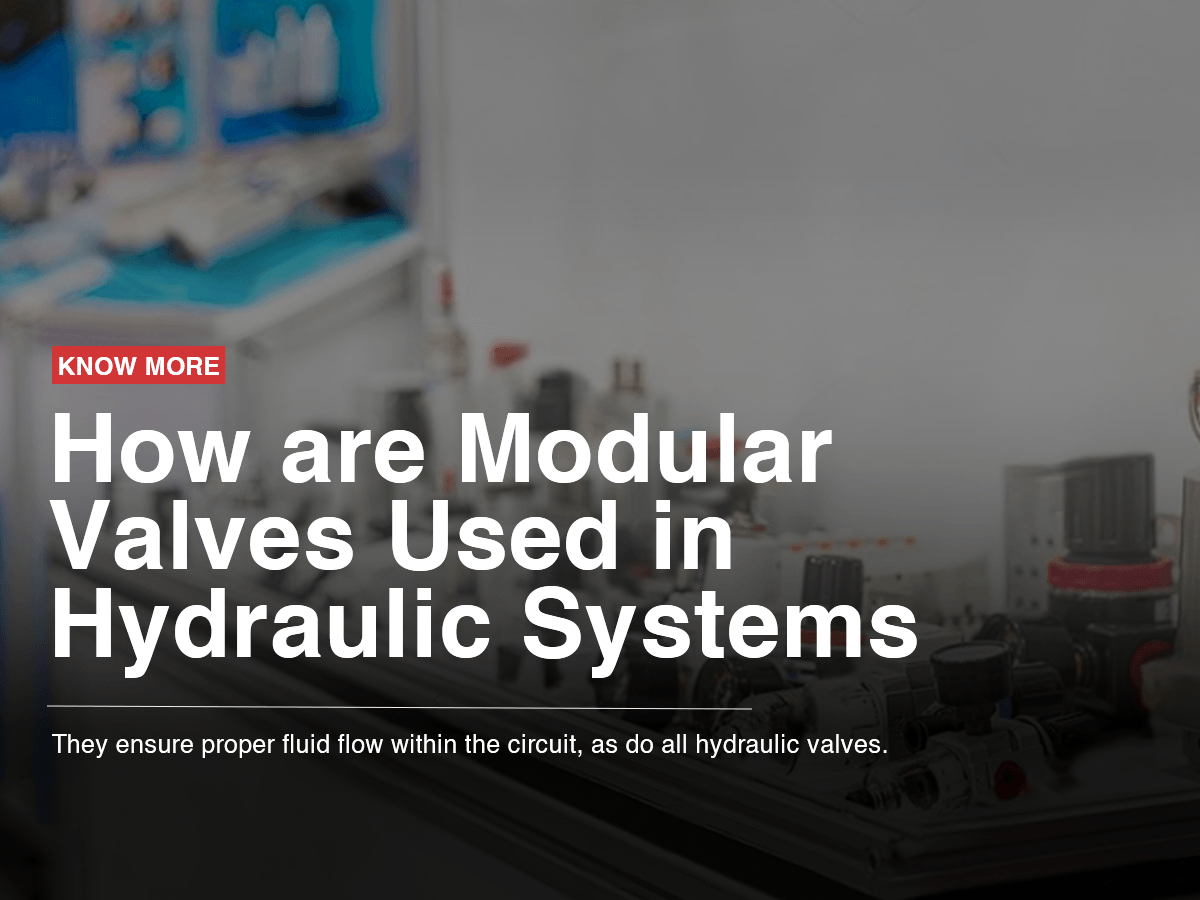
How are Modular Valves Used in Hydraulic Systems
The majority of modern hydraulic systems utilize modular valves, which play a crucial role in ensuring proper fluid flow within the circuit, much like other hydraulic valves. Effective regulation of the direction, speed, and force of hydraulic fluid flow is essential to prevent issues such as overloading, under-pressured lines, and fluid retention within the machine's circuit. Modular valves offer additional advantageous properties beyond their ability to control one-way fluid flow as seen in traditional individual valves.
The term "modular valve" refers to a valve securely encased and installed onto a base plate of a specific size, protected by a plastic box paneling that safeguards against particulate infiltration and wear. Unlike fixed valves that are typically installed as in-line components in hydraulic fluid lines, modular valves feature designated inputs and outputs at fixed locations that connect quickly to O-rings. This characteristic allows easy and safe reorganization, testing, and repair of the hydraulic circuit by swapping out identical-size modular housing. Consequently, defective modular units can be replaced promptly, saving valuable time, effort, and expenses.
Moreover, modular hydraulic valves can be combined to create a manifold block. This innovative approach provides hydraulic designs with increased flexibility by sequentially altering the flow rate and volume of hydraulic fluid through various modular valves. The use of a modular valve manifold eliminates the need for additional connecting pipes, a significant contributing factor to hydraulic failures.
There are four primary categories of modular valves:
-
Pressure Control - The most common type of modular valve is the pressure-regulating one, which analogously reduces the fluid inflow per second by limiting PSI at a specific location in the machine. It effectively prevents pressure overload in pipes and cylinders during actuation movements, motion peaks, spikes, and unexpected surges. Some valves feature movable screws that allow adjustments to the valve's fluid resistance.
-
Flow Control - Similar to pressure regulators, flow control valves facilitate safe omnidirectional hydraulic motor usage and are particularly useful for recirculating fluid back into the reservoir. These valves prevent backflow while restricting flow to the direction of travel with the most power, up to a critical PSI.
-
Pressure Checkers - Pressure check valves are adept at pumping fluid back into the reservoir, acting similarly to pressure regulators in enabling secure omnidirectional hydraulic motor use. They restrict flow to the direction of travel with the most power while preventing backflow, up to a critical PSI.
-
Reversible Shuttle - Equipped with digital, electronic control systems, reversible shuttle valves offer the capability to instantly integrate up to all three functions into the system. They find application in industrial systems requiring rapid reconfiguration, which justifies their designation as "shuttle" valves.