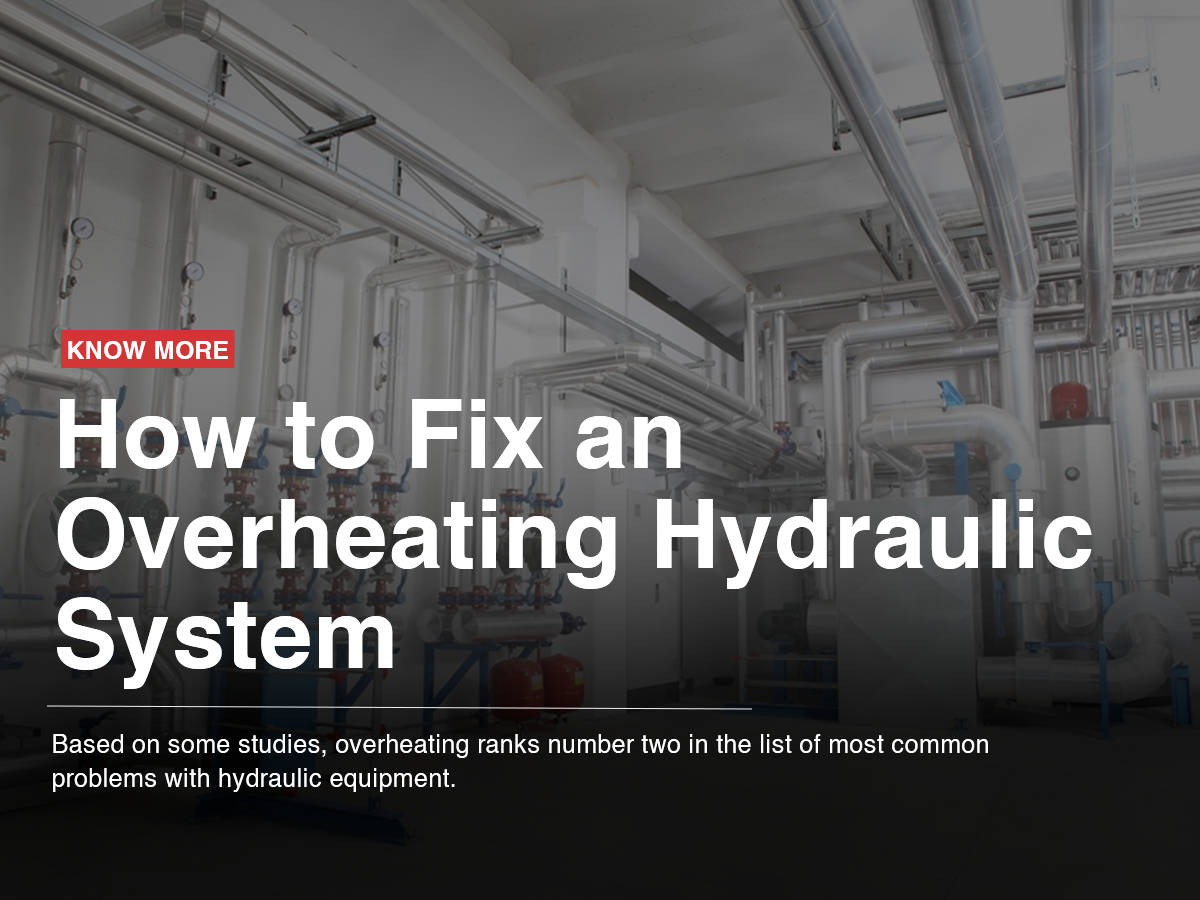
How to Fix an Overheating Hydraulic System
According to various studies, overheating is the second most common issue faced by hydraulic equipment, and understanding the root causes and effective solutions for this problem is essential. In this article, we aim to delve into the reasons behind hydraulic system overheating and explore potential remedies.
The Generation of Heat due to Pressure Drop: Heat is generated whenever hydraulic fluid flows from a high-pressure area to a low-pressure area without producing mechanical work, resulting in a pressure drop. Several factors can influence the amount of pressure drop experienced, including friction, fluid type and temperature, length and size of the hose assembly, type of couplings and adapters, and the flow rate. Conducting a thorough Pressure Drop Analysis allows for effective control of pressure drop within the system.
Suggested Solutions:
-
Upsize the components and reduce plumbing bends: To mitigate pressure drop and subsequent heat generation, consider increasing the size of hoses and fittings, particularly in areas with radical bends. By doing so, the flow capacity can be significantly improved. For instance, transitioning from #10 SAE hydraulic hose to #12 SAE hose can reduce flow restriction, leading to a 25% decrease in heat load and a subsequent increase in hydraulic system efficiency.
-
Increase heat dissipation: In order to stabilize oil temperature, the hydraulic system must have the capacity to dissipate heat that exceeds its inherent heat load. Inefficiencies in the system can result in the conversion of input power (PL) into heat, contributing to the problem. Employing appropriately sized heat exchangers can effectively remove excess heat from the hydraulic system. The size of the heat exchanger required is proportional to the total power losses of the system, which can be challenging to calculate due to numerous unknown variables. However, some general rules of thumb for sizing heat exchangers are as follows: a. Simple circuit with minimal valves: 25% b. Simple circuit with cylinders: 25% c. Simple circuit with fluid motors: 31% d. Hydrostatic transmissions: 35 - 40% e. Servo-based systems: 60 - 75% f. Low-pressure fluid transfer: 15%
In Conclusion: Whenever a hydraulic system experiences overheating, it is crucial to promptly shut it down, identify the root cause, and apply the necessary fixes. Continuing to operate a hydraulic system while the fluid is overheating can lead to damage and should be avoided at all costs. By understanding the causes of overheating and implementing appropriate solutions, hydraulic equipment can operate optimally and maintain efficient performance.