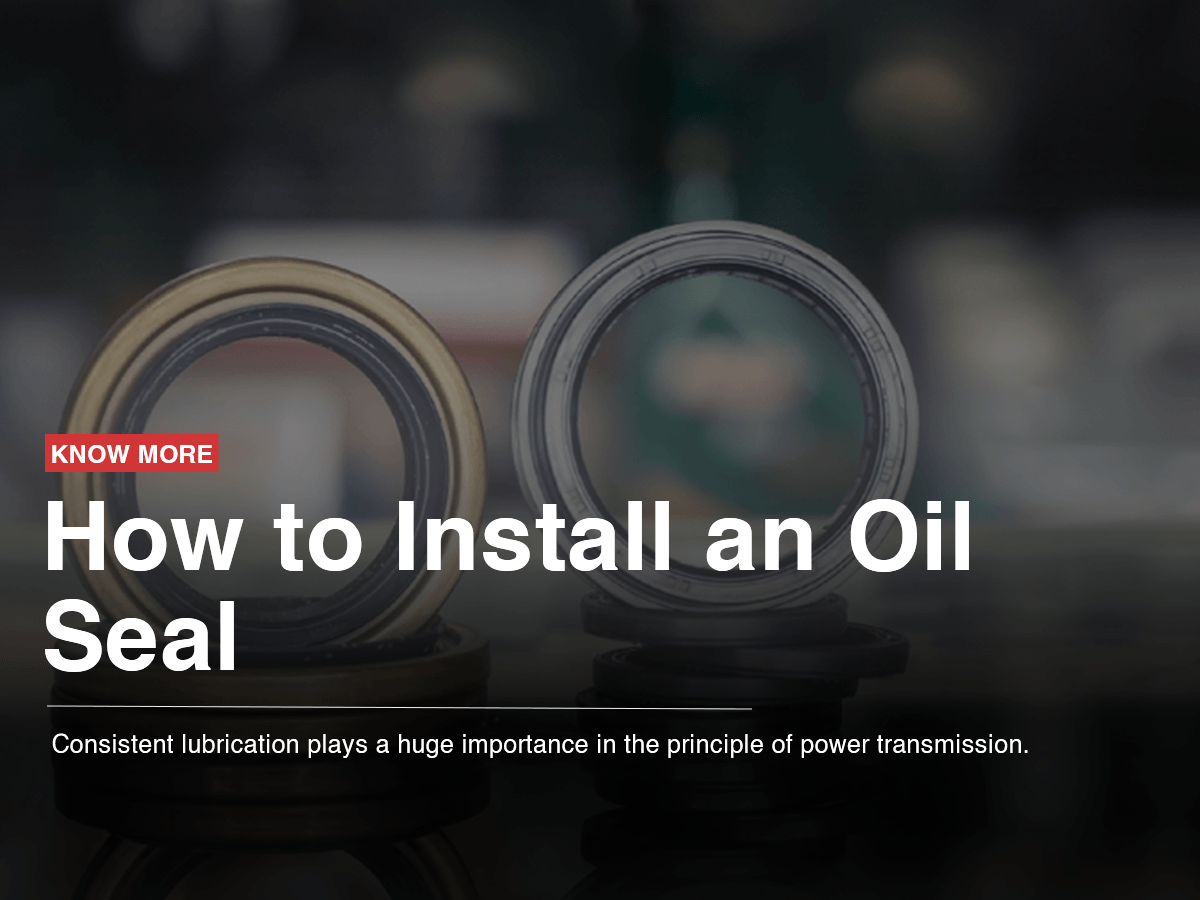
How to Install an Oil Seal
A consistent and effective lubrication process is of utmost importance in power transmission principles. In various scenarios involving a shaft-mount reducer, such as an electric motor prime mover driven by belts and motion controlled by a torque arm, shaft seals play a critical role. An improperly seated seal can lead to severe consequences, including a blown-out input shaft, necessitating a complete breakdown, reassembly, realignment, and re-tensioning of the belts. Hence, the oil seal serves as the primary defense in keeping lubrication inside the reducer and preventing contaminants from entering the system.
The basic oil seal consists of a case, lip/lips, and a garter spring. Proper installation is essential to ensure its quiet and efficient operation behind the scenes of the application.
Preparation for Oil Seal Installation: Before commencing the installation process for any power transmission component, meticulous cleaning is imperative to eliminate any material flaws such as nicks, burrs, scratches, or dents. This attention to detail is especially crucial for oil seals, considering their function. Additionally, inspect all relevant surfaces, including the shaft sealing surface, housing bore, seal lip(s), and outside diameter. Preserving the integrity of the sealing lips is of utmost priority, as they may wear over time due to pressure, leading to potential lubricant leakage and particulate ingress.
Addressing Seal Lip Wear: To address potential seal lip wear, several solutions can be applied. If sufficient room is available in the housing bore, a spacer may be used to shift the seal forward. Alternatively, shaft repair sleeves can be employed to provide a "new surface" to the shaft, covering flaws and allowing proper contact with the seal. As a last resort, shaft replacement or refinishing may be necessary.
Oil Seal Installation Process: During the installation process, ensuring the correct positioning of the spring seats within the seal is an essential initial step. Applying a small amount of grease to the seal lip(s) and the area of the shaft in contact with the seal is recommended. For double-lip seals, filling the small cavity between the lips with grease offers protection during initial installation and break-in. For rubber-coated seals, lubricant applied to the outside diameter helps prevent the seal from rebounding or dislodging during mounting. Proper alignment of the seal is crucial, with the sealing lip facing the lubricant requiring sealing. In the case of double lip oil seals, the second lip, serving as a dust lip, should be installed perpendicular to both the shaft and housing bore.
Importance of Proper Installation: Angular misalignment or cocking of the seal on the shaft can result in an irreversible process and premature failure. Ensuring the seal is correctly installed avoids excessive pressure on specific sections of the seal, potential dislodging of the spring, or overheating and brittleness due to wear.
Tools Required During Installation: For a successful oil seal installation, specific tools are recommended. An installation sleeve aids in passing gears and splines safely without compromising the seal's integrity. A hammer, used for the final step of the installation, applies uniform force to the seal case, ensuring it seats flush. A strike plate is utilized to accurately cover the entire seal during the installation process.
Conclusion: The effectiveness and quiet operation of the installed component serve as indicators of a successful oil seal installation. Proper techniques, diligence, and attention before, during, and after the installation process result in a well-lubricated and efficiently operating power transmission component.