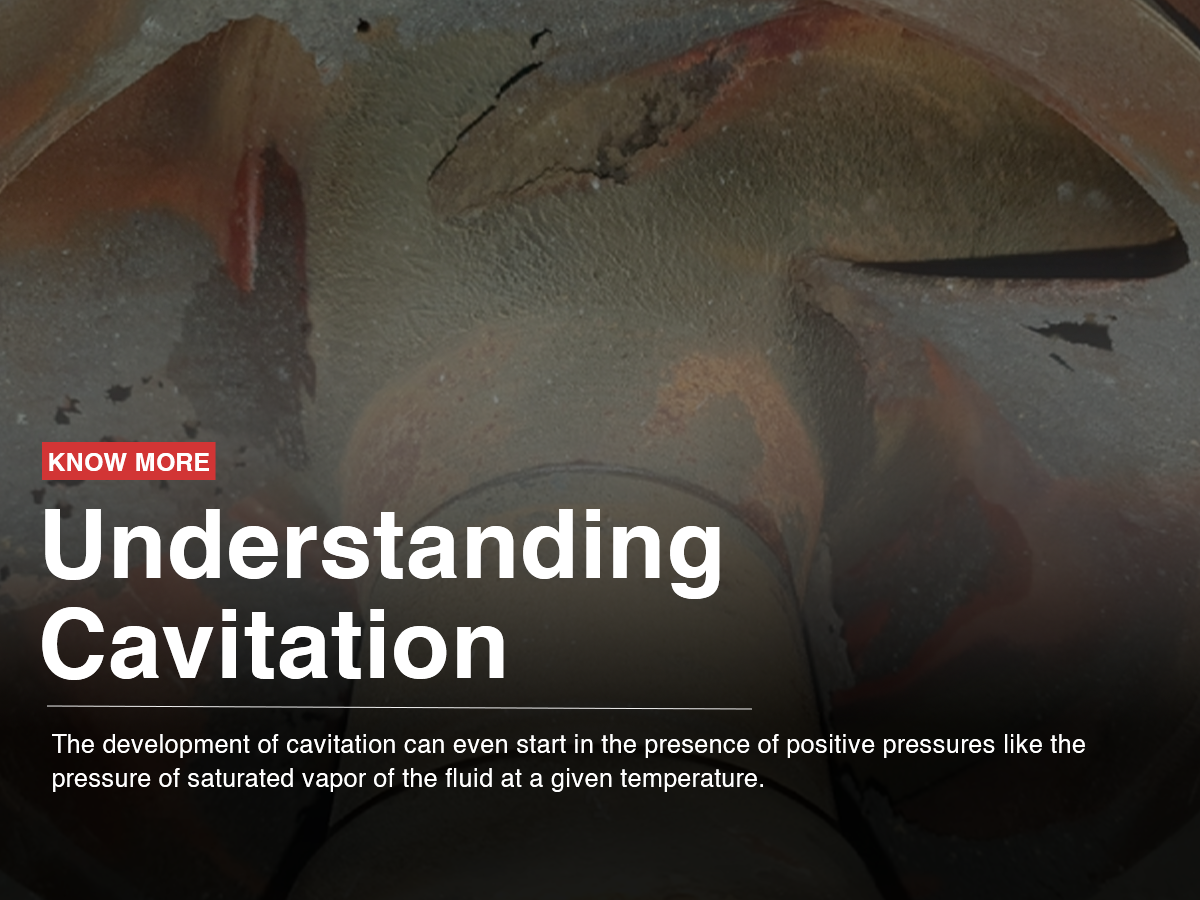
Understanding Cavitation
Cavitation can occur even in the presence of positive pressures, such as the pressure of saturated vapor at a given temperature. The degree of resistance to cavitation varies among different liquids and depends largely on the concentration of gas and foreign particles present in the liquid.
The cavitation nuclei consist of gaseous or vaporous bubbles that serve as reservoirs for vapor or dissolved gases when the pressure reaches a certain level. As these bubbles enter a zone of reduced pressure, they condense, leading to a rapid process accompanied by local hydraulic shocks, sound emission, material bond destruction, and other undesirable phenomena. The wear mechanism associated with cavitation involves surface destruction and material displacement due to high relative motions between a surface and the exposed fluid.
Cavitation can be categorized into vaporous cavitation, where bubbles grow explosively as the pressure drops below the liquid's vapor pressure, and gaseous cavitation, where cavitation wear does not occur, but high temperatures and chemical degradation of the fluid can happen.
Cavitation wear, also known as cavitation erosion or pitting, is a fluid-to-surface type of wear. It occurs when a portion of the fluid experiences tensile stresses that cause boiling and subsequent compressive stresses that lead to the collapse of vapor bubbles. This collapse generates mechanical shocks and microjets that impact the surfaces, causing damage.
The occurrence of cavitation can be audibly and visually detected, and its effects can lead to extensive damage in materials. The extent of cavitation damage depends on the pressure and velocity of the collapsed bubbles. Various components in hydraulic systems are prone to cavitation wear, including control valves, pump suction chambers, actuators, and leakage paths.
To identify cavitation sources in a fluid system, factors such as low pressure (vacuum), high temperature, and air ingression should be considered. Possible locations to check for air ingression include reservoirs, pumps, valves, actuators, motors, accumulators, filters, and conduit connectors.
To prevent cavitation-related issues, proper system design, control of flow restrictions, and the use of original replacement parts are essential. Maintenance and adherence to fluid cleanliness are also crucial in avoiding cavitation damage and ensuring the longevity of hydraulic systems.