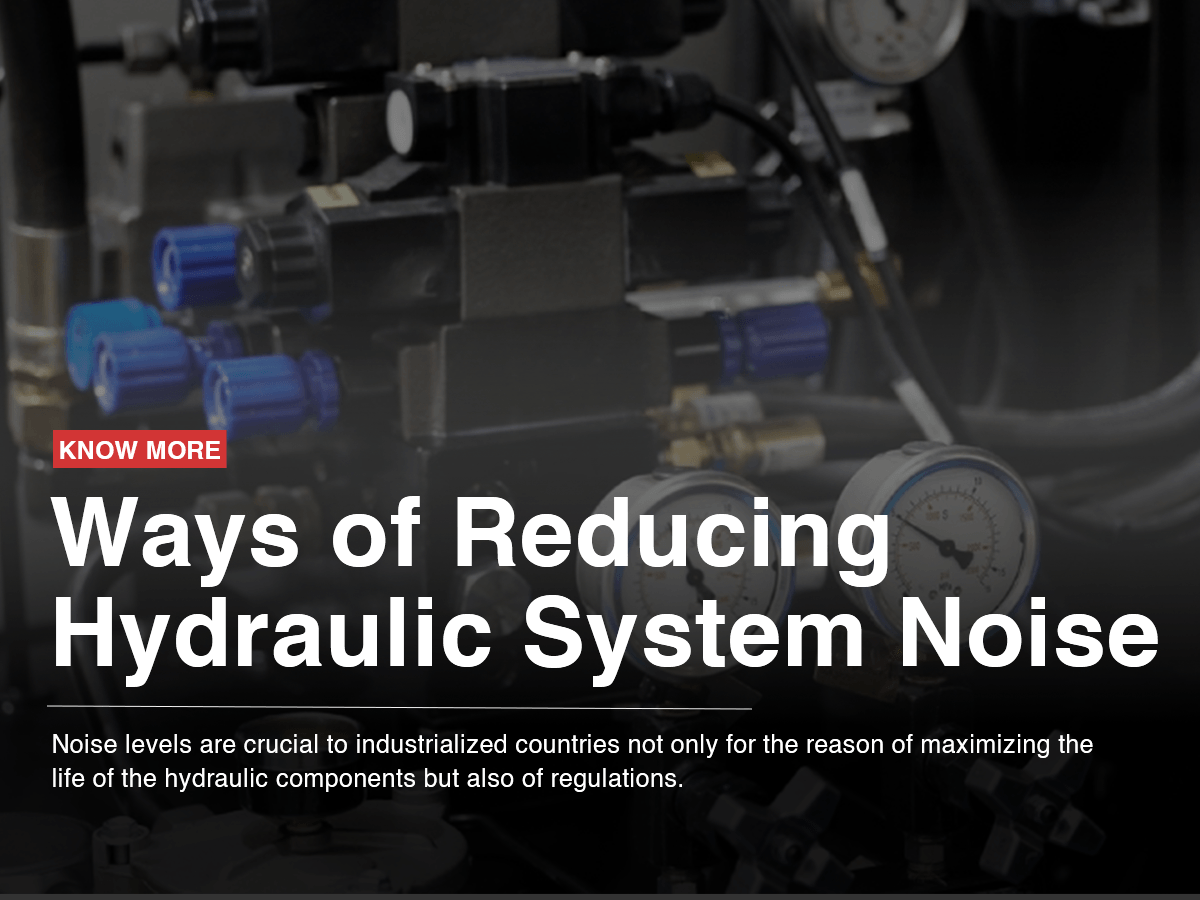
Ways of Reducing Hydraulic System Noise
Noise levels are of paramount importance in industrialized countries, not only for maximizing the lifespan of hydraulic components but also for complying with regulations. The primary source of noise is typically the hydraulic pump, which transmits structure-borne, fluid-borne, and air-borne noise. One classic example is positive-displacement hydraulic pumps, which generate pressure pulsations due to their specific pumping chamber design and continuous cycle operation.
To reduce fluid-borne noise caused by pressure pulsations, a silencer installation is a common solution in large hydraulic systems or noise-sensitive applications. The reflection silencer is a straightforward type that eliminates sound waves by generating supplemental sound waves with the same amplitude and frequency but at a 180-degree phase angle to cancel out the original waves.
Structure-borne noise is often found in the hydraulic pump and its prime mover (power unit) due to vibrations. This can be mitigated by eliminating sound bridges through the use of flexible connections like rubber mounting blocks and hoses. In certain cases, introducing more mass to the system can reduce vibration transmission.
Air-borne noise can be minimized by reducing the object's surface area or increasing its mass. For instance, constructing the hydraulic reservoir with thicker plates can decrease its noise radiation. Mounting the hydraulic pump inside the tank and incorporating decoupling between the power unit and tank can also help reduce air-borne and structure-borne noise.
Hydraulic fluid has energy storage capabilities due to its compressibility. To prevent sudden energy release that leads to noise and stress on conductors and system components, decompression must be controlled whenever the volume change exceeds 10 cubic inches (160 cubic centimeters). This can be achieved by metering the compressed fluid across an orifice to convert potential energy into heat.
Water hammer, a phenomenon caused by sudden changes in fluid velocity within a pipe, can lead to high noise levels, vibration, and pipe damage. Accumulators can partially resolve this issue, but the most effective approach is to reduce the fluid velocity by increasing the pipe diameter, thus minimizing the magnitude of stored energy and the sudden pressure rise during its release. By considering these strategies, industrial facilities can effectively manage and reduce noise levels, promoting a conducive and compliant working environment.