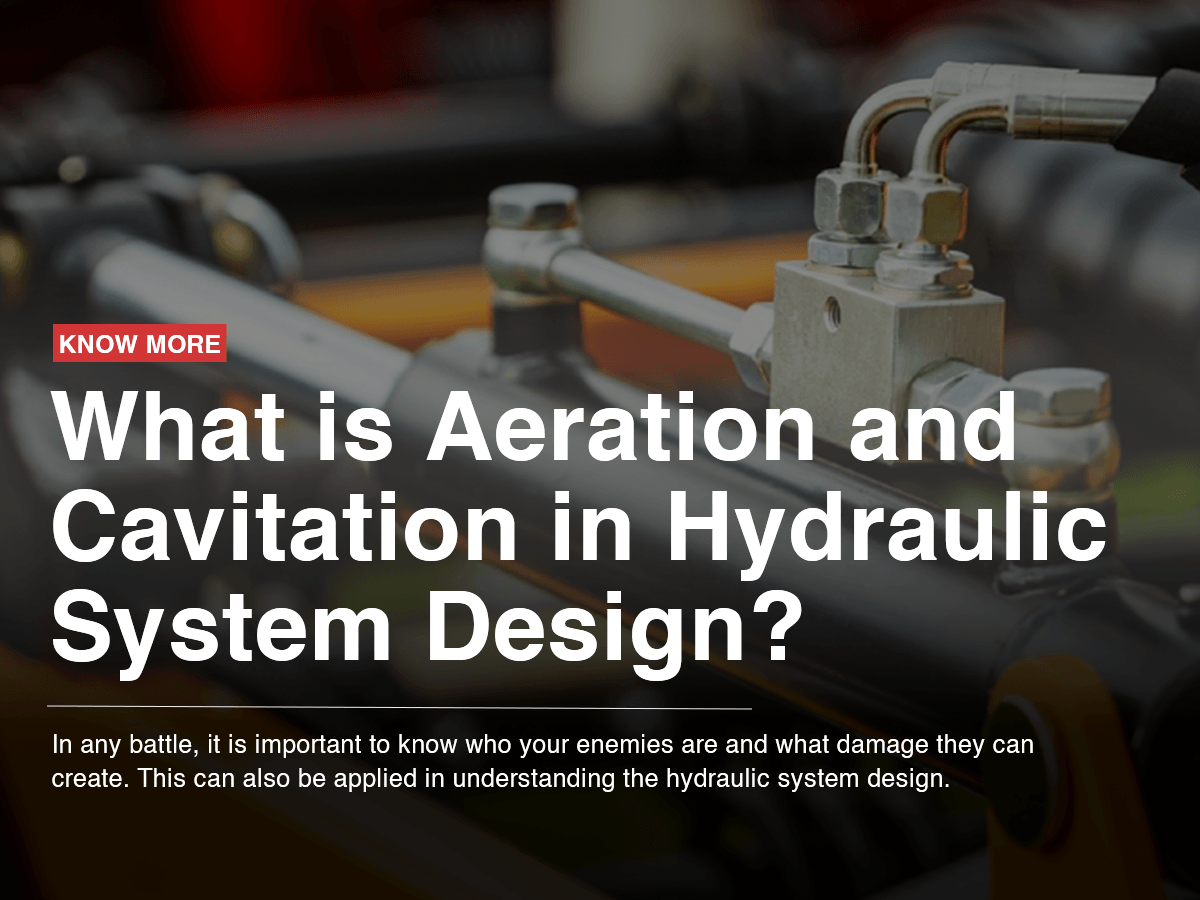
What is Aeration and Cavitation in Hydraulic System Design?
In any battle, it is crucial to identify adversaries and understand the potential damage they can inflict. This principle applies to the hydraulic system design, where we must address the issues of aeration and cavitation. Aeration occurs when air is mixed with or dissolved in the hydraulic fluid, often caused by air leakage from pump seals, pipe fittings, and unions. This can lead to fluid degradation, resulting in damage to system components due to loss of lubrication, overheating, and seal burning.
Cavitation, on the other hand, involves the formation of gas bubbles that create vapor cavities in the liquid. Rapid pressure changes of these gas bubbles cause shock waves, leading to implosion near metal surfaces. This inertial cavitation causes surface fatigue and damage to metal surfaces. To prevent cavitation, it is essential to slow the fluid flow through the system to avoid the occurrence of NPSHA.
Both aeration and cavitation share common symptoms, including abnormal noise such as banging or knocking when air circulates through the system under varying pressures. Moreover, high fluid temperatures above 180°F (82°C) can result from factors like low reservoir levels or increased heat load due to compressed air, harming system operation and damaging seals. The loss of flow and erratic actuator and valve movement are additional indicators of aeration and cavitation.
The consequences of cavitation are severe and include damage to system components, fluid contamination, and mechanical failure. It frequently occurs at the pump in hydrodynamic situations, making it essential to keep the pump suction line unobstructed.
Improper designs that contribute to aeration and cavitation include controlled fluid flow to the pump, loose fittings or connections on the suction line, low hydraulic fluid levels or NPSHA, excessive pump speed, incorrect fluid viscosity, foaming oil, blocked reservoir air breather vent, excessively low oil temperature, and worn pumps.
Unresolved cavitation can lead to significant damage and expensive downtime for hydraulic systems. To prevent such issues, proper maintenance and system design are critical. Careful monitoring of the hydraulic system can provide early detection of potential problems.