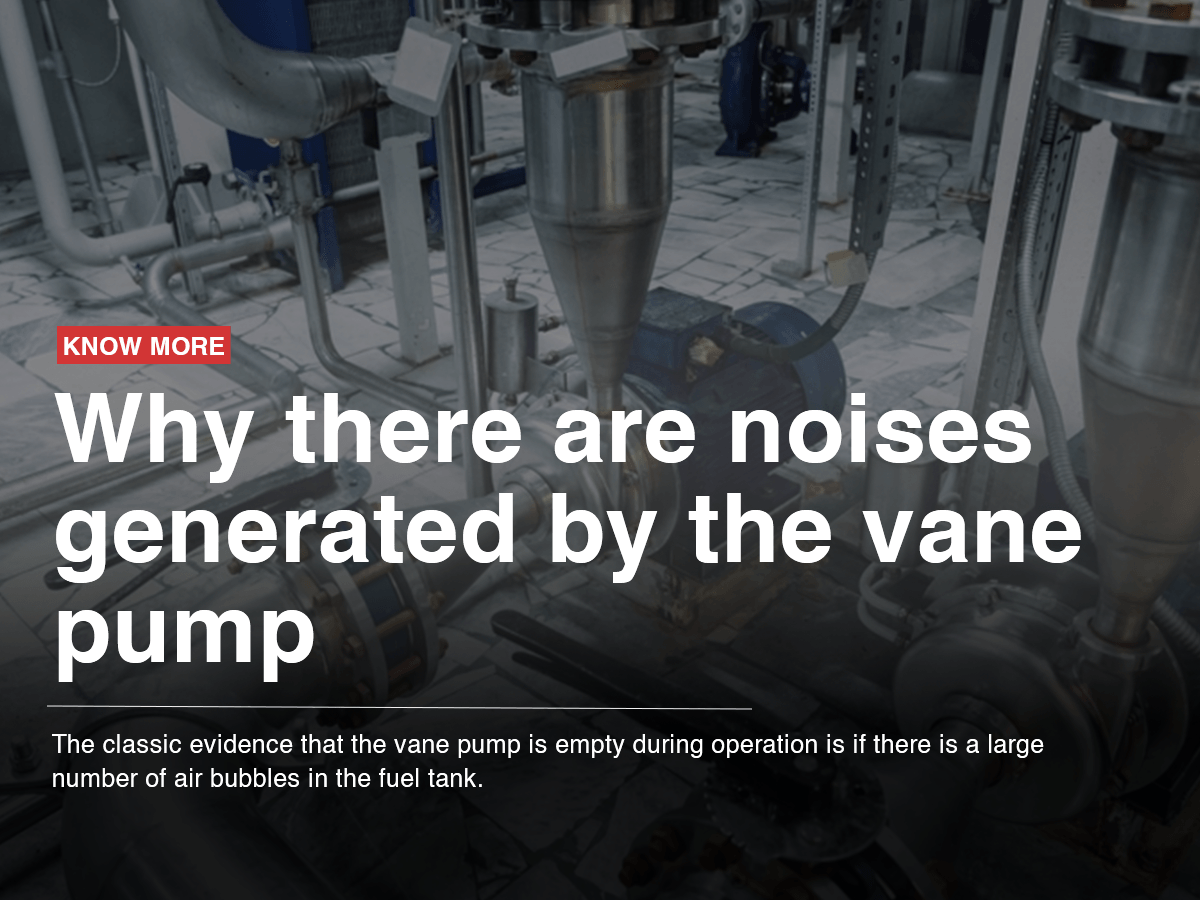
Why there are noises generated by the vane pump
The noise generated by the vane pump can be attributed to several primary reasons:
- The vane pump operating while empty, allowing air to enter the pump body. This can be identified by the presence of numerous air bubbles in the fuel tank. To address this, it is crucial to check the hydraulic oil level, inspect the filter for deformation, and clean the hydraulic oil as needed.
To clean the hydraulic oil, you can temporarily remove the filter to see if the issue is resolved. Investigate potential problems with the seal of the inlet pipe, check for crushed seals at the pump casing connection during direction changes, and examine the shaft seal for signs of aging or damage. Note that for new pumps, blisters may be present in the pump casting even after resolving these issues.
- Damage to the pump core components can also contribute to the noise. To verify this, a thorough inspection of the pump core components, such as the upper and lower oil distribution plates, rotor, stator, and blades, is necessary. Common causes of damage include inadequate oil pumping capacity, hydraulic oil pollution, mismatched clearances between the oil disc and rotor, and issues with the output shaft and pump motor.
a. Reasons for rotor wear:
- Insufficient oil pumping capacity of the vane pump.
- Critical pollution of the hydraulic oil, leading to the entry of large chemical particles into the pump body.
- Inadequate matching clearance between the blades and the oil disc due to material inconsistencies in the pump core components.
- Pulsation and eccentricity of the pump core rotor caused by misalignment between the output shaft and motor.
b. Reasons for stator wear and blade fracture:
- Elevated system oil temperatures, preventing the formation of a protective oil film between the stator and the blade.
- Severe hydraulic oil pollution with large chemical particles.
- High viscosity of the hydraulic oil, causing inadequate blade smoothness during operation and leading to uneven blade deformation and fracture.
- Inadequate selection and heat treatment of the stator and blade, resulting in reduced toughness and potential pressure shock-induced blade breakage.
- Untight bearing and shaft seal can lead to leakage. This issue may arise due to improper installation of the vane pump output shaft and motor output shaft, system pressure fluctuations, or incorrect assembly during high-speed pump operation.
To prevent relief valve failure and potential hazards, adding a secondary safety relief valve, along with a pressure sensor or over-pressure warning mechanism, is recommended. This secondary relief valve should limit the system pressure slightly above the working pressure to avoid damaging components in case the primary relief fails.
Selecting the correct relief valve involves considering various factors such as size, design (spring relief, direct-acting, or pilot-operated), and control mechanism (solenoid or PLC-controlled).
For a safe and efficient system design, the expertise of Cross Company's team of engineers and field sales representatives can be relied upon, from initial conceptualization to complete installation.