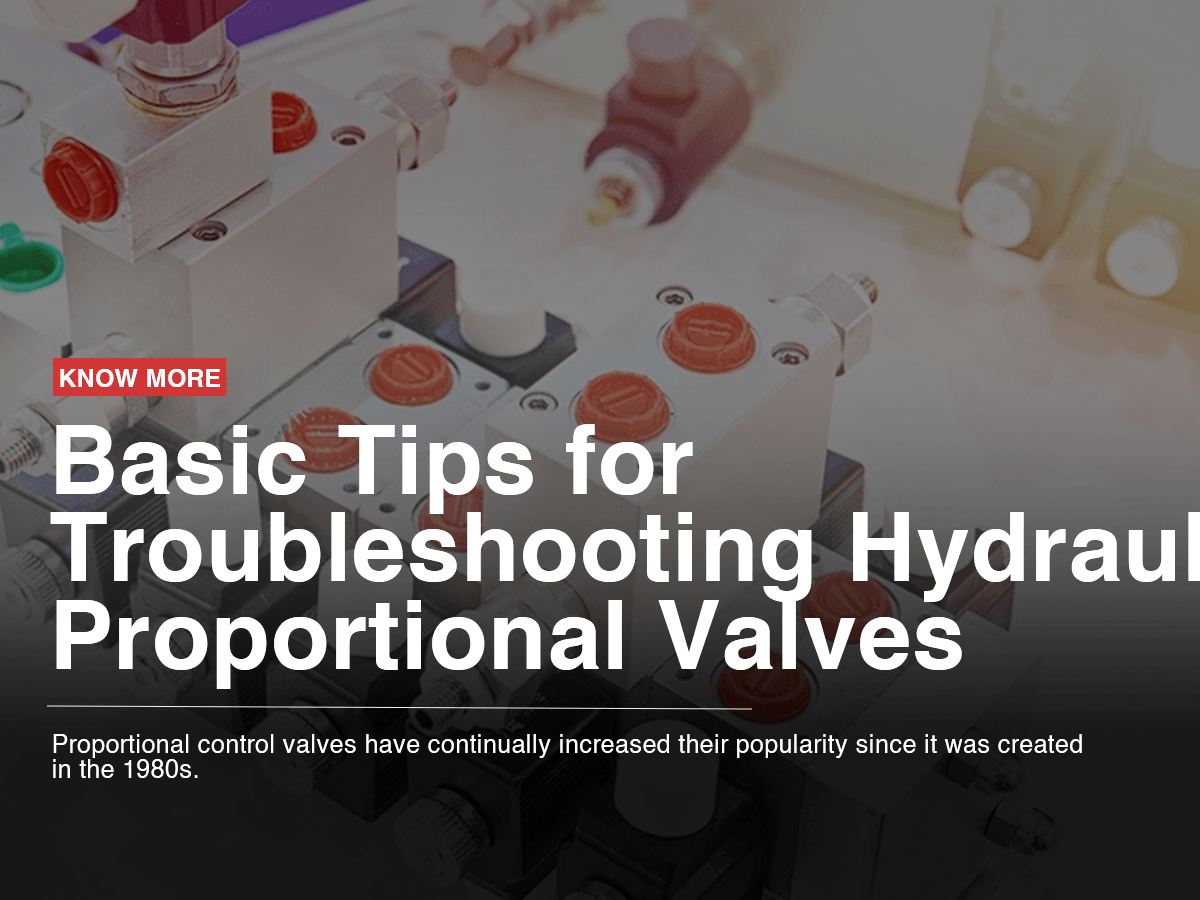
Basic Tips for Troubleshooting Hydraulic Proportional Valves
Proportional control valves have witnessed a steady rise in popularity since their inception in the 1980s. Due to the significant cost difference between servo valves and proportional control valves, the latter has found widespread adoption in various applications, replacing servo valves in many cases. Proportional valves are commonly used as directional, flow, and pressure control valves. Irrespective of the manufacturer, all proportional directional valves essentially serve the same purpose: to control the direction and speed of hydraulic cylinders or motors. On the other hand, servo valves continue to play a crucial role in larger equipment such as aircraft and turbine generators.
The components of a proportional valve include the spool, solenoid, and linear variable differential transformer (LVDT). To operate the valve, a power supply and amplifier are essential. The power supply powers the amplifier, typically operating at 24 volts, while the command voltage from the programmable logic controller (PLC) determines the valve spool's position. The enable signal, sent via a relay from the PLC, is necessary to send a current to the proportional valve coil.
When troubleshooting hydraulic proportional valves, it is generally a straightforward process. For externally mounted amplifier setups, front panel lights indicate any issues with the system. By tracing back from these lights, potential problems can be identified and resolved. For instance, if the "on" light fails to turn on, the power supply voltages at the amplifier connections should be checked. If there is no input voltage, the wiring and output signal from the PLC should be examined. A red light indicates that the power supply voltage has dropped below a minimum threshold.
Maintaining proper oil cleanliness is crucial for proportional valves due to their tight tolerances between the spool and housing. The oil must meet the manufacturer's standards to prevent system failure, damage to internal components, and other issues. The International Organization for Standardization (ISO) sets the cleanliness standards for oils used in specific valves, which necessitates regular oil sampling to ensure compliance.
By adhering to these troubleshooting tips and ensuring oil cleanliness, production downtime and unnecessary expenses for valve repair and maintenance can be minimized effectively.