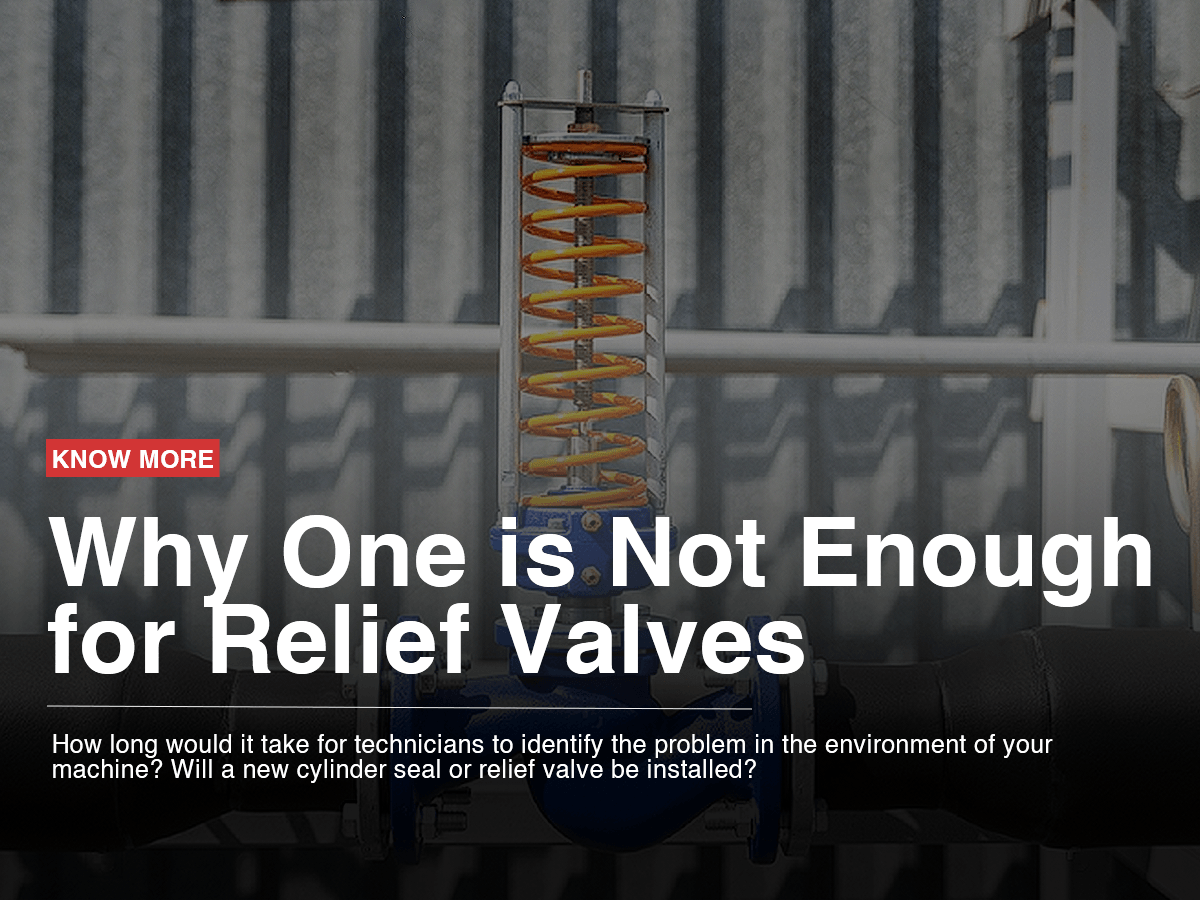
Why One is Not Enough for Relief Valves
Hydraulic oil is highly efficient in performing a vast amount of work, but without safety relief valves, it can lead to severe damage to pumps, motors, hoses, and fittings, which are typically the weakest components in the system.
It is essential for every hydraulic system to include at least two relief valves: a primary and a backup. The primary relief valve ensures that the system does not operate above a specific pressure, while the backup relief valve, typically set 200-300 psi higher than the primary relief, will open in case of primary relief failure.
A common scenario of relief valve failure can occur in mobile systems where pressure relief is integrated into control valves for individual working stations. If a rupture occurs in an internal seal, causing a clog in the hydraulic valve, the relief valve may fail to open, leading to potential explosions in hose connections and hazardous hydraulic fluid leakage.
Preventing such failures can be achieved by incorporating a secondary safety relief valve, ideally with a pressure sensor or over-pressure warning mechanism. The secondary relief valve would limit the system pressure slightly above the working pressure, preventing catastrophic failures and allowing operators to detect inefficiencies early on.
Selecting the correct relief valve involves considering various factors, such as the valve's size, design (spring relief, direct-acting, or pilot-operated), and the control mechanism (solenoid or PLC-controlled).
Cross Company's team of engineers and field sales representatives can provide expertise in designing safe and efficient hydraulic systems, from conceptualization to full installation. Clients can rely on us to ensure a safe and clean system design for their hydraulic applications.