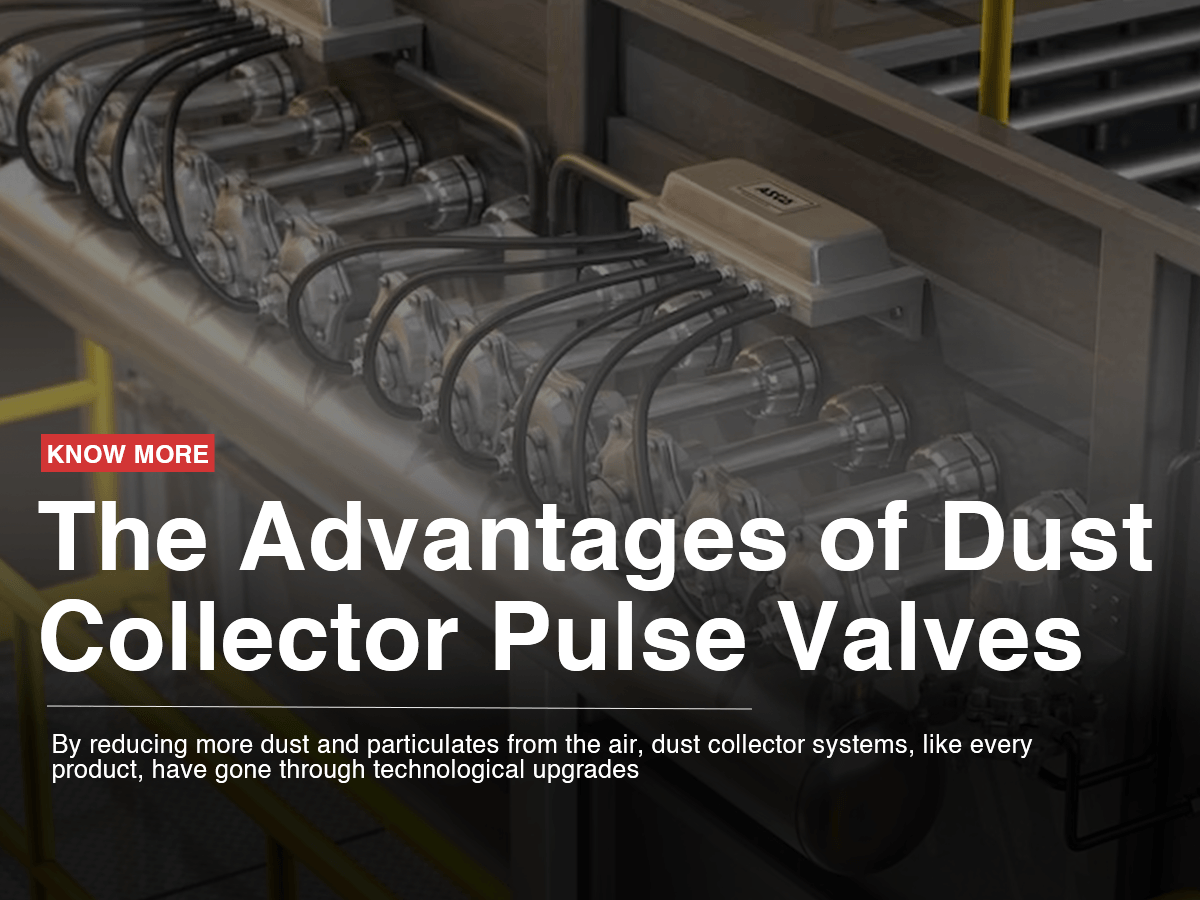
The Advantages of Dust Collector Pulse Valves
Dust collector systems have undergone significant technological upgrades and innovative modifications to address the growing need for reducing dust and particulates from the air. Industries like concrete, metalworking, mining, steel mills, grain, agriculture, and feed, where particulate contamination can cause costly equipment damage and downtime, have shown particular interest in these advancements. Additionally, dusty environments, especially in the food and beverage industries, pose health risks to workers. To combat these challenges, specific equipment designed for handling, storage, and drying operations is commonly used in these industries. As an added measure, industries handling cereal, protein powder, and starch products have been incorporating aggressive anti-bacterial chemicals to reduce food contamination risk, though careful consideration is essential due to the potential adverse effects on equipment over time. While dust collector systems are beneficial for most industries, certain sectors, such as automotive factories, chemical producers, and power plants, that generate a substantial volume of particulates, require specialized solutions.
Efficient dust collection in automated applications necessitates using equipment that can withstand various materials, including aggressive agents. Companies must prioritize the incorporation of highly effective dust collector systems to minimize maintenance concerns. Pulse valves play a crucial role in these systems, cleaning bag-type or cartridge-type filters. Employing high-energy pulses of air through blow tubes creates shock waves down the filters, effectively removing dust particles. Pulse valves with higher air acceleration and quicker response time contribute to superior filter cleaning and reduced compressed air consumption, thereby optimizing system operation costs. It is advantageous for pulse valves to generate high peak pressure blasts of air, ensuring efficient dust collection filter bag cleaning and extending filter life. In contrast, inadequate peak pressure and slow response time can lead to subpar filter cleaning and wasted compressed air, compromising both operational costs and market standing.
Key attributes sought in pulse valve design by OEMs, engineers, purchasing managers, and end-users include robust performance, reliability, and user-friendliness. Today's favored pulse valves offer a simplified design that maximizes valve performance, resulting in extended system uptimes. Specifically tailored for filter cleaning in dust collectors and baghouses with reverse pulse jet systems, these valves require high peak pressure, high flow rates, long life, and extremely fast valve opening and closing for effective filter cleaning while minimizing compressed air waste. Some pulse valves are engineered to provide long operating life, surpassing one million cycles.
For practical pulse valve design, various connection options, such as threaded, dresser, and quick-mount, facilitate faster, easier, and more secure installation, benefiting both initial setup and replacement scenarios. Flexibility in valve orientation without affecting operation is desirable, and built-in silencers are essential for reducing noise and preventing foreign particle ingress. Compliance with strict safety regulations, especially in hazardous or explosive environments, requires pulse valves to meet global approvals like UL, CSA, RoHS, ATEX, CE, and others. Working with a company offering optional waterproof and explosion-proof solenoids for use in potentially hazardous atmospheres and recommending extended temperature ranges is recommended to ensure safety and reliability.
When selecting pulse valves, addressing diverse concerns is critical for various stakeholders, including OEMs, engineers, and purchasing managers. Beyond technological advancements, factors like seamless integration with existing systems, longevity, low maintenance requirements, and compatibility with other components influence buying decisions. Excellent technical support and prompt delivery are vital for ensuring smooth operations. Same-day shipping with guaranteed product availability is particularly important for preventing downtime, especially for OEMs.
In conclusion, technological advancements have significantly improved dust collector systems, addressing critical issues related to dust and particulate removal. By incorporating highly efficient pulse valves and considering various practical and solution-solving attributes, industries can enhance the performance, longevity, and cost-effectiveness of their dust collector systems. Furthermore, the adoption of these advancements contributes to improved worker safety, equipment protection, and regulatory compliance.