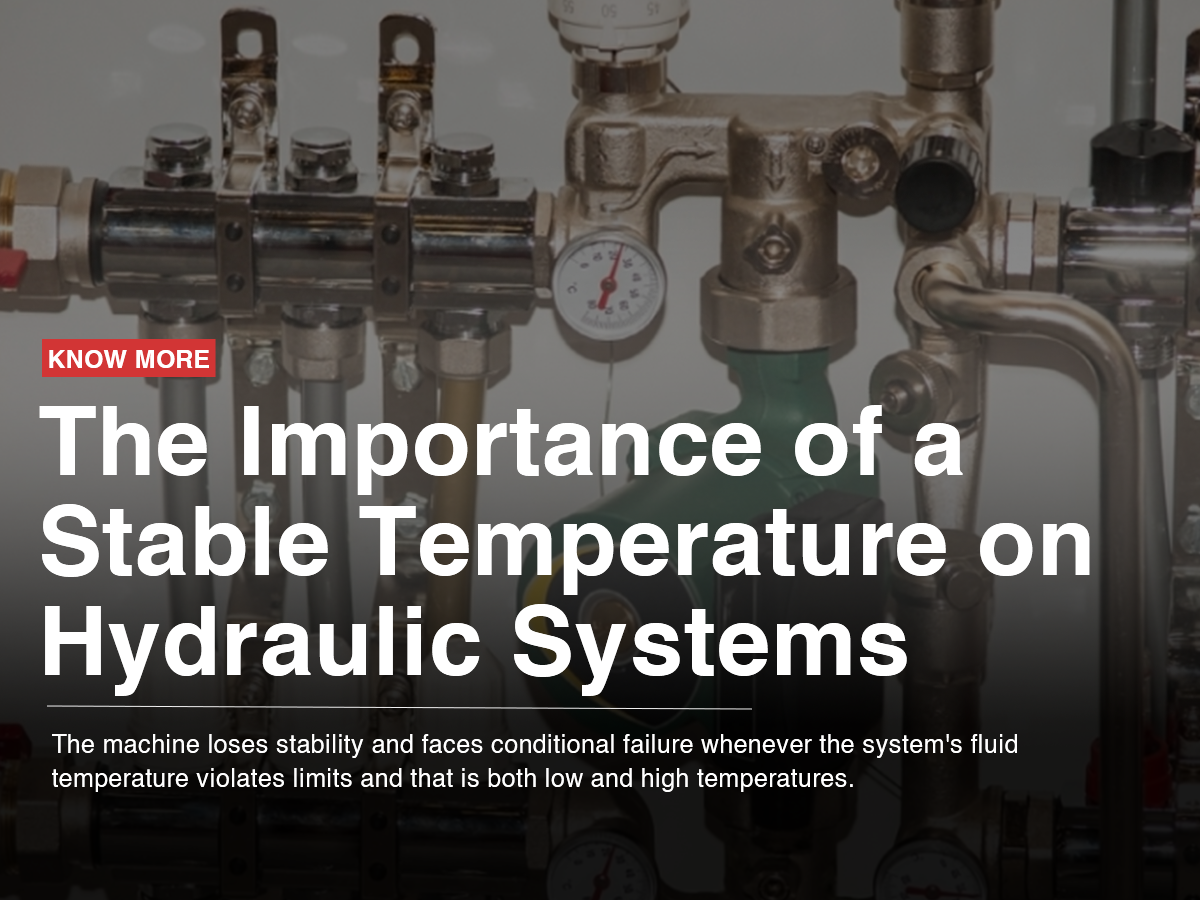
The Importance of a Stable Temperature on Hydraulic Systems
The stability of a machine is compromised, and conditional failure becomes a concern when the fluid temperature in the system exceeds both low and high limits. Fluid temperature stability is a critical factor in ensuring the success of mechanical systems. In hydraulic systems, whether large or small, a thorough investigation of temperature instability can help uncover its effects on machine operation, leading to performance enhancements and increased equipment service life. Various factors contribute to fluid temperature instability, including component integrity (design, selection, manufacture, application, and maintenance), duty cycle severity (load application, magnitude, and duration), environmental hostility, and heat absorption/desorption.
Low temperatures can be equally damaging to the temperature stability of hydraulic fluids as high temperatures. In cold environments or high-altitude conditions, petroleum-based fluids may experience an increase in viscosity, reaching a critical point where the fluid thickens and ceases to flow. This can lead to issues such as pump starvation, damaging vaporous cavitation, increased fluid and mechanical friction, and lubricant starvation of bearing surfaces. The lubrication effectiveness of a fluid at low temperatures depends on its viscosity and pour-point characteristics.
On the other hand, high temperatures are a more common problem that can disrupt the stability of conventional working fluids, negatively impacting system performance and reducing the lifespan of operating components. In systems exposed to hostile environments and severe duty cycles, the need for supplemental heat transfer capability and/or synthetic fluids may become apparent.
High temperatures can cause permanent damage, including a reduction in fluid viscosity accompanied by mechanical rubbing and increased temperature. Poor shear stability of a fluid encountering high temperatures can lead to irreversible viscosity changes. The impact of high temperature on oil properties is severe, promoting rapid oxidation, sludge formation, and accelerated component wear.
Heat generation in fluid systems arises from converting mechanical energy or fluid pressure energy, and its source must be identified to prevent damage to the hydraulic system. High friction in the system can be caused by improperly lubricated components, the use of fluids with incorrect viscosity, pressure-activated piston seals, fluid passing through constricting orifices at high speed, or flowing through restricted passages.
Failure to achieve and maintain fluid temperature stability within an appropriate range throughout the operating period can lead to serious damage to the fluid system. A heat balance analysis is crucial in troubleshooting systems facing abnormal conditions, such as high ambient temperatures, high altitude, low suction line pressure, or localized external heating.
In conclusion, improper fluid temperature can trigger a chain reaction leading to total system failure. High-temperature operation significantly affects the wear of bearing-type surfaces in a system, necessitating strict precautions to prevent costly equipment damage. Monitoring and maintaining fluid temperature stability are paramount to ensuring the efficient and reliable performance of hydraulic systems.