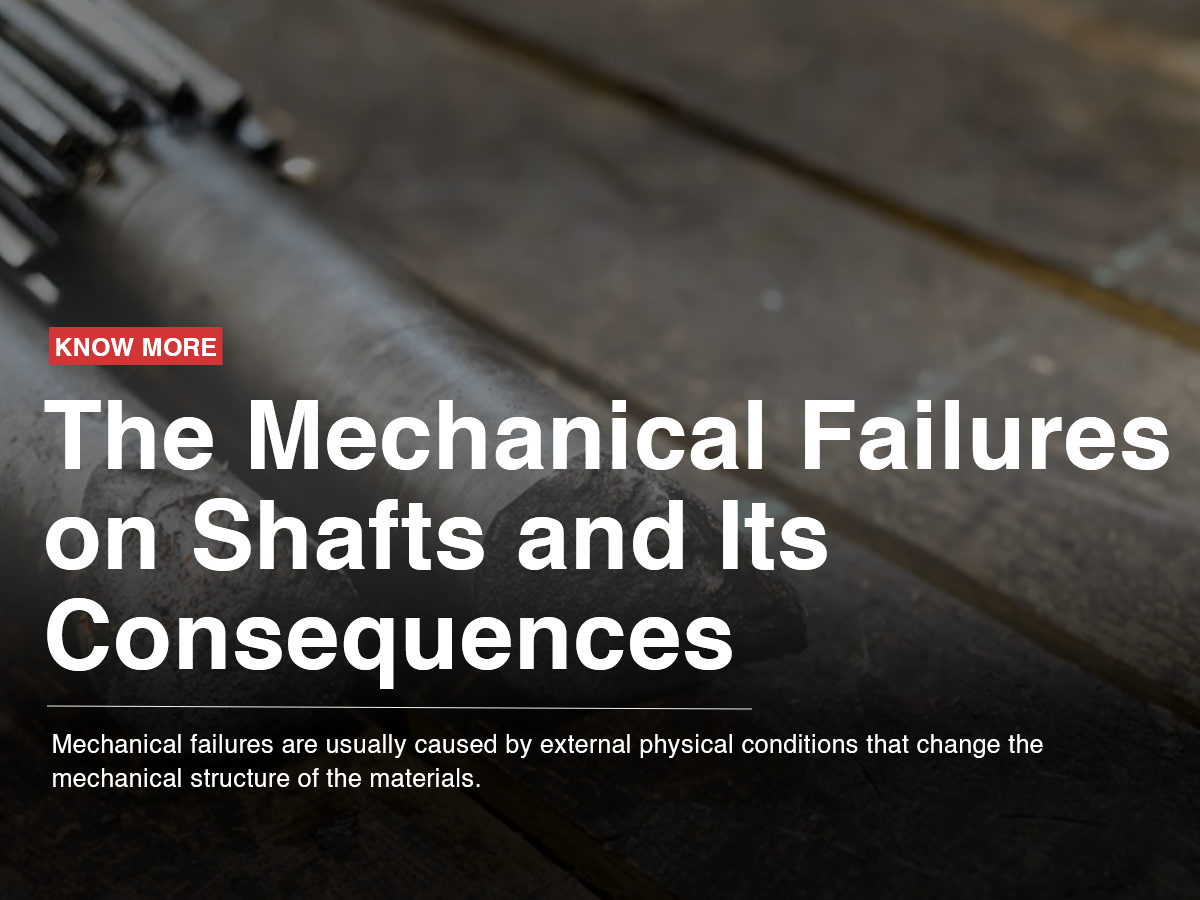
The Mechanical Failures on Shafts and Its Consequences
Mechanical failures in hydraulic systems often result from external physical conditions that cause changes to the mechanical structure of materials. These incidents commonly involve axial and radial shaft overloads, rotary bending (flexion), and torsion (twisted) fatigue failures. Understanding the root causes of these failures is crucial in devising strategies to prevent them.
Here is a list of common mechanical failures:
-
Shaft Problems: These are often caused by poor alignment and incorrect mechanical links, such as bracket or chassis deformation, improper bell housing, and loosely fitted damping elements. Other contributing factors may include:
- Insufficient gap between coupling flanges (axial loads/radial loads) or unbalanced coupling.
- Excessive load on a belt-driven system (belt drives not recommended).
- Non-homokinetic transmission due to an unbalanced Cardan shaft or universal joint, leading to inconsistent shaft speed.
- High moment of inertia caused by heavy couplings (e.g., chain couplings) or couplings with large diameters.
- Bracket deformation under load.
- Hose strain force due to abrupt pressure compression or decompression.
- Strain from rigid pipe mounting.
- Input torque exceeding limits.
-
Bad Shaft/Coupling Connection: This issue often arises due to mispositioning, such as:
- Incorrectly positioned locking screw on a keyed shaft.
- Improper machining of couplings.
- Inadequate tolerance fit between shaft and coupling diameter.
- Misalignment of keyway in the coupling with the main bore axis.
- Improperly engaged shaft (e.g., insufficient surface contact for spline or key use).
- Poor or absent lubrication of splined shafts/couplings.
- Mispositioned dowel pin in the cartridge.
- Improper mounting of cartridge screws.
-
Hollow Push Pin Misalignment: This problem occurs when the pin is mistakenly installed upside down in T6*M mobile cartridges.
-
Loose Fasteners: Failure to properly tighten assembling screws after pump modification can lead to problems.
-
Marks on Port Plates: Even minor scratches or marks between the inlet and pressure areas can disrupt the pump's cycle and destabilize the vanes.
CONSEQUENCES:
The severity of mechanical failures determines the resulting damages to hydraulic components:
-
Fretting Corrosion: Occurs under high solicitations and slight vibration movements, leading to metallic oxides that weaken the component's structure and initiate fatigue rupture (twisted).
-
Worn Shaft Splines/Keyed Shafts: This can occur along the total length or part of the length due to fatigue.
-
Fatigue Shaft Rupture: Different types of fatigue ruptures include perpendicular, centered, rotational bending fatigue rupture; perpendicular, over-centered rotational bending fatigue rupture; twisted torsional rupture; and perpendicular, torsional fatigue rupture.
-
Bush/Bearing Problems: Issues may involve heavy wear on front or rear bearings, bush "welding" on the shaft, rear bush moving out of the rear port plate, and damaged front ball bearings.
-
Marked Cam Ring: Marks on the cam ring due to rotor contact may create local tensions or cracks if the contact is critical.
-
Losing Contact on Shaft Seal: Air intake and leakage can lead to the loss of contact on the shaft seal.
-
Dissymmetrical Wear on Port Plates: Tilted vanes can cause parallel marks on the port plate, even if the pump is not rotating.
Understanding and addressing these mechanical failures are essential in maintaining the efficiency, reliability, and longevity of hydraulic systems.