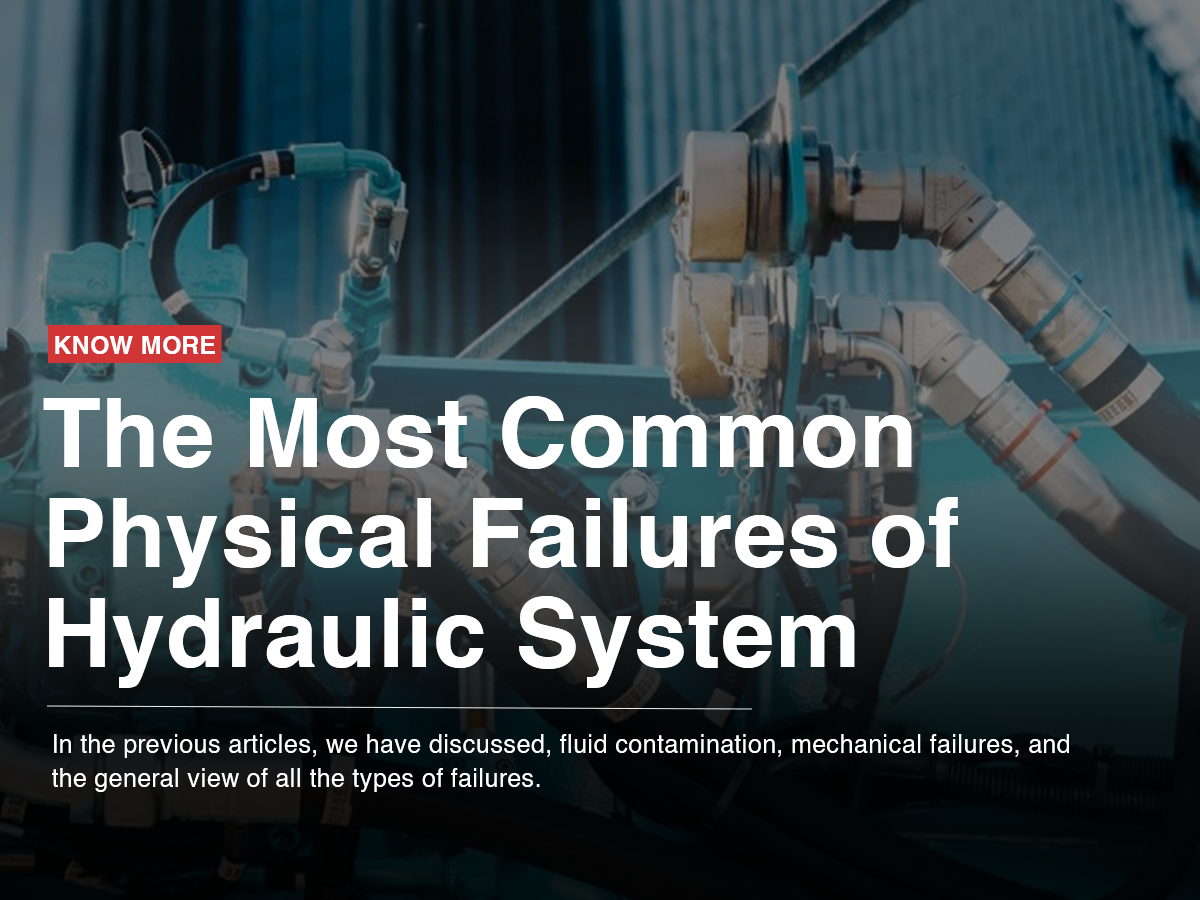
The Most Common Physical Failures of Hydraulic System
In the preceding articles, we have extensively covered fluid contamination, mechanical failures, and various types of failures. It is evident that most of these failures are interconnected, often stemming from the quality of the lubricant, inadequate filtration, or unfavorable inlet conditions.
In this article, we will focus on physical failures and provide relevant troubleshooting and precautionary measures.
-
Start-up Without Proper Air Bleed-off: Before operating the pump, it is crucial to prime the circuit and ensure complete air bleed-off. Failing to do so can result in pump damage due to insufficient lubrication and hindered pump performance.
-
Air Contamination - Fluid Foaming: a. Aeration: This occurs when air is introduced into the system, causing the fluid to lose its standard hydraulic fluid capabilities. Aeration can be caused by various external factors, such as a suction pipe not properly sealed, deteriorated shaft seal, inadequate inlet tube positioning, insufficient suction surface for turbulence, and others. The consequences of aeration include unbalanced vanes, severe damage, and noisy pump operation. b. Cavitation-Daeration: This involves the formation of small bubbles under depression or vacuum conditions, leading to shock waves and erosion (cavities) when compressed above their critical pressure. External causes of cavitation-daeration include clogged suction strainer, excessively long inlet hose, inadequate tank volume, and poor tank deaeration capabilities.
-
Solid Particle Contamination: The hydraulic circuit is highly sensitive to pollution and is often the first component to fail. Metallic oxide, silica, and organic materials can enter the system, causing damage to vanes, cam ring, rotor, port plates, and other components.
-
Water Contamination: Water contamination and its consequences are covered in another article, Fluid Contamination Incidents and Their Consequences.
-
Viscosity Failures: Viscosity, influenced by temperature, plays a significant role in these failures. When viscosity is too high, vanes may stick in the rotor slots, resulting in no flow. On the other hand, low viscosity can cause scars on port plates and rotor, or even lead to seizure due to excessive cavitation. The choice of viscosity index, filterability, oxidation resistance, daeration capabilities, and pollution control are essential considerations.
-
Unsuitable Grease: For heavy-duty applications, it is recommended to use grease lubricants based on disulfide or molybdenum.
Understanding and addressing these physical failures is crucial in maintaining the optimal performance and reliability of hydraulic systems. By implementing the appropriate troubleshooting and preventive measures, operators can mitigate potential damages and extend the equipment's lifespan.