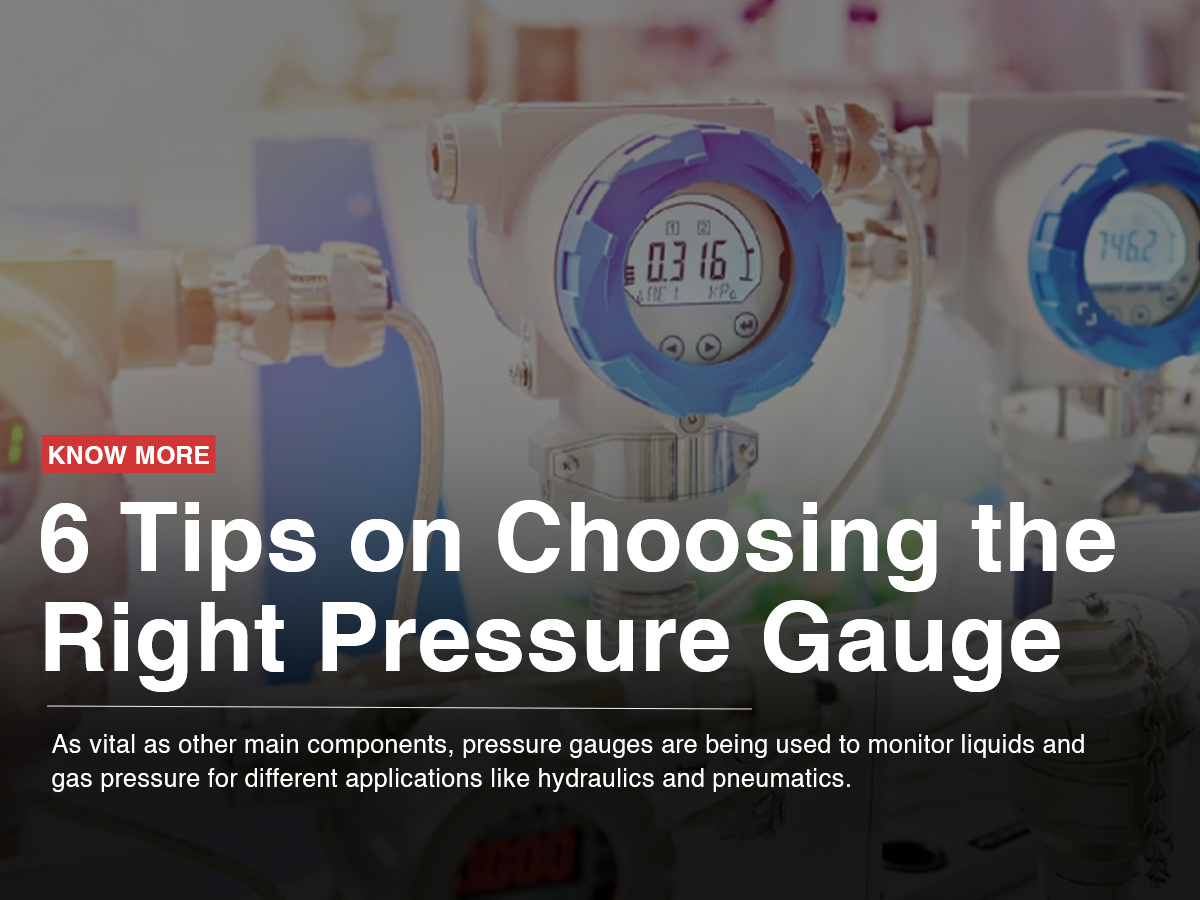
6 Tips on Choosing the Right Pressure Gauge
Pressure gauges play a crucial role in monitoring liquid and gas pressure across various applications, such as hydraulics and pneumatics, medical settings, pumps and compressors, refrigeration controls, utilities, and gas monitoring. Utilizing pressure gauges contributes not only to the smooth flow of operations but also enhances the longevity of the company's components. When deciding on a pressure gauge, the initial consideration is whether to opt for digital or mechanical variants. In many industrial processes, the digital pressure gauge's high level of accuracy and additional features may not be necessary, making mechanical pressure gauges more practical. Here are some factors to keep in mind when choosing the appropriate mechanical pressure gauge:
-
Size - Selecting the right size depends on factors like readability, available space, and precision requirements. Larger dial faces provide more gradations for precise readings and easier visibility from a distance. The size of the end connection is also important in determining the gauge's size.
-
Temperature - Consider both ambient and media temperature to determine the suitable material for the wetted parts. For lower ambient temperatures, a liquid-filled gauge is preferable. In cases where the media temperature exceeds 140°F (60°C), a stainless steel gauge should be used.
-
Application - The industry and specific application will influence the type of pressure gauge needed. For sanitary processes, gauges with hygienic designs are necessary. Certain applications may require special approvals, such as UL (Underwriter Laboratories) and FM (Factory Mutual) approvals for gauges used with fire sprinklers. In high-vibration environments, liquid-filled gauges are recommended to dampen movement and safeguard the instrument's internal mechanism.
-
Media - Consider the nature of the substance flowing through the pipeline. The media also impacts the type of case-filling required. Brass gauges suit non-aggressive liquids or gases like water and air. Corrosion-resistant materials, such as stainless steel or nickel-copper alloys like Monel®, are essential for handling harsh chemicals like sour gas (hydrogen sulfide), ammonia, and creosote.
-
Pressure - When evaluating pressure, three questions come to mind: the type of pressure to be measured (gauge pressure, absolute pressure, or differential pressure), the operating range of the application, and the desired pressure scale.
-
Ends (Process Connections) - Consider the process connections, their sizes, and their locations when selecting a pressure gauge.
There is a diverse range of options and accessories available to choose from when selecting a pressure gauge. Despite its seemingly simple nature, reviewing these factors is crucial in finding the right type of pressure gauge and accessories that align with your specific application requirements.