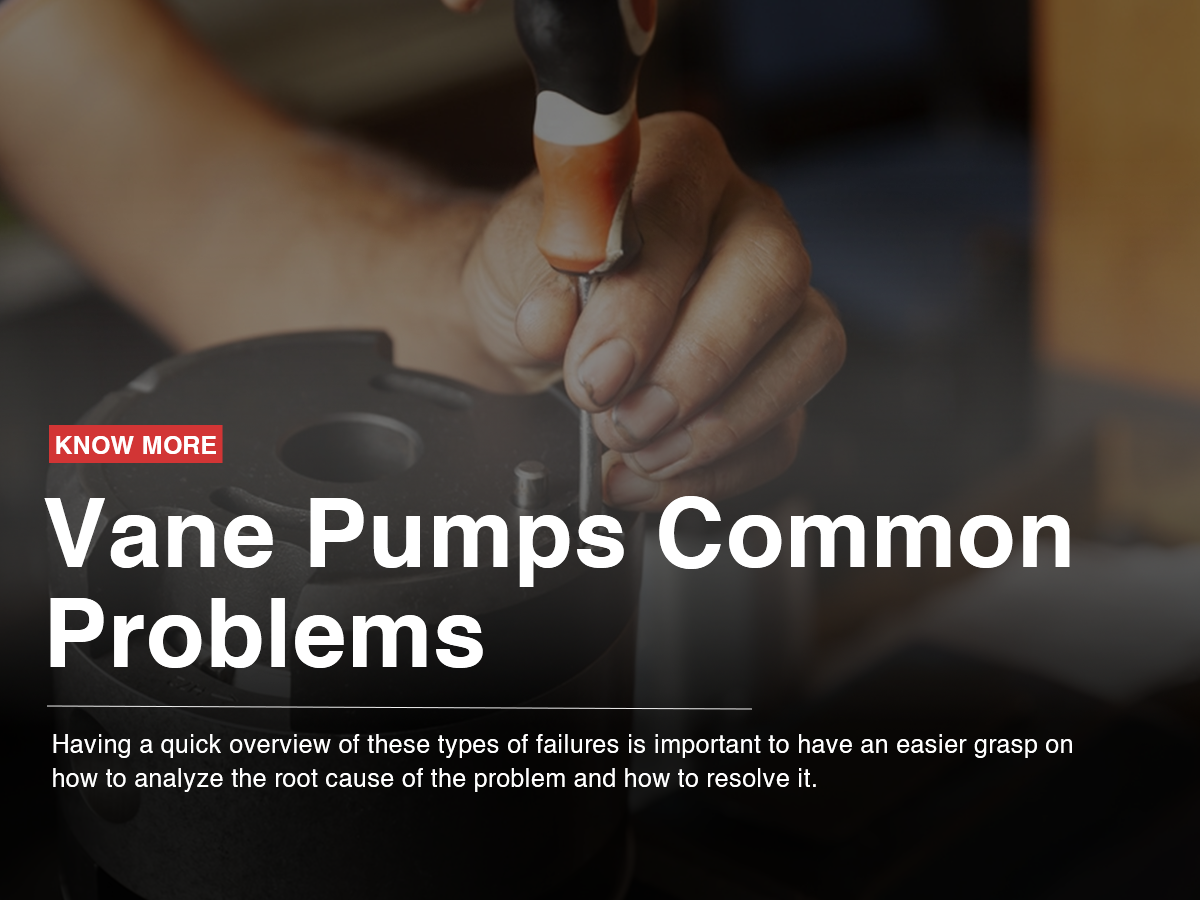
Vane Pumps Common Problems
Gaining a comprehensive understanding of the various types of failures is crucial for effectively analyzing the root causes of problems and finding appropriate solutions. Identifying the cause enables us to pinpoint mechanical issues that led to the failure. To expedite this process, a vane troubleshooting guide has been prepared to provide a swift and satisfactory conclusion.
-
Mechanical Failures: These failures arise from external physical conditions that alter the mechanical structure of materials. They are typically attributed to axial and radial shaft overloads, rotary bending (flexion), and torsion (twisted) fatigue failures. Common problems include misalignment in shafts, improper shaft/coupling connections, mispositioned dowel pins in the cartridge housing, incorrectly mounted cartridge screws, and loose fasteners. Care must be taken during reassembly to ensure proper engagement of the rotor and vanes in the cartridge. Incorrectly mounted hollow push pins and marks on port plates may also contribute to these failures.
-
Pressure Failures: Pressure overshoot can be categorized into "instant pressure overshoot" and "cycled overpressurization." Both result in pressure peaks that can reach 2 to 5 times the adjusted maximum pressure valve, leading to component failures. Instant pressure overshoot causes abrupt high peaks of pressure, resulting in failures such as cracked or ruptured pressure port plates, split rotors, cracked cam rings, broken shafts, and cut dowel pins. Cycled overpressurization is a long-term fatigue failure affecting components such as cam rings, vanes, shafts, side plates, and rotor splines, with consequences including ruptured cam rings, worn-out shaft internal splines, shaft rupture, and deformed port plates.
Pressure gradients can induce sudden pressure changes, altering internal pump leakage and potentially leading to phenomena like cavitation and hose decompression. This can cause fatigue rupture of cam rings and seizures of rotors and port plates.
- Physical, Chemical, or Hydraulic Failures: Start-up without proper air bleed-off results in inadequate lubrication due to a lack of priming, leading to local overheating and pump malfunction. Air contamination can cause fluid foaming, turning it black with a burnt smell, known as the "Lorentz" or "Diesel" effect. Solid particle contamination, although not applicable to Parker vane units, is a significant cause of pump destruction. It can lead to rapid wear or premature breakdown.
Water contamination affects fluid characteristics, impacting pump performance. Deposits on vanes alter pump efficiency, fluctuating fluid compressibility destabilizes vanes, and viscosity changes can result in deaeration or erosion on port plates. Unsuitable grease or lubricants not based on disulfide or molybdenum can cause issues, and using inappropriate fluids can lead to various problems, considering parameters like viscosity index choice, filterability, oxidation resistance, deaeration capabilities, polluted fluid density, and fluid deterioration over time.