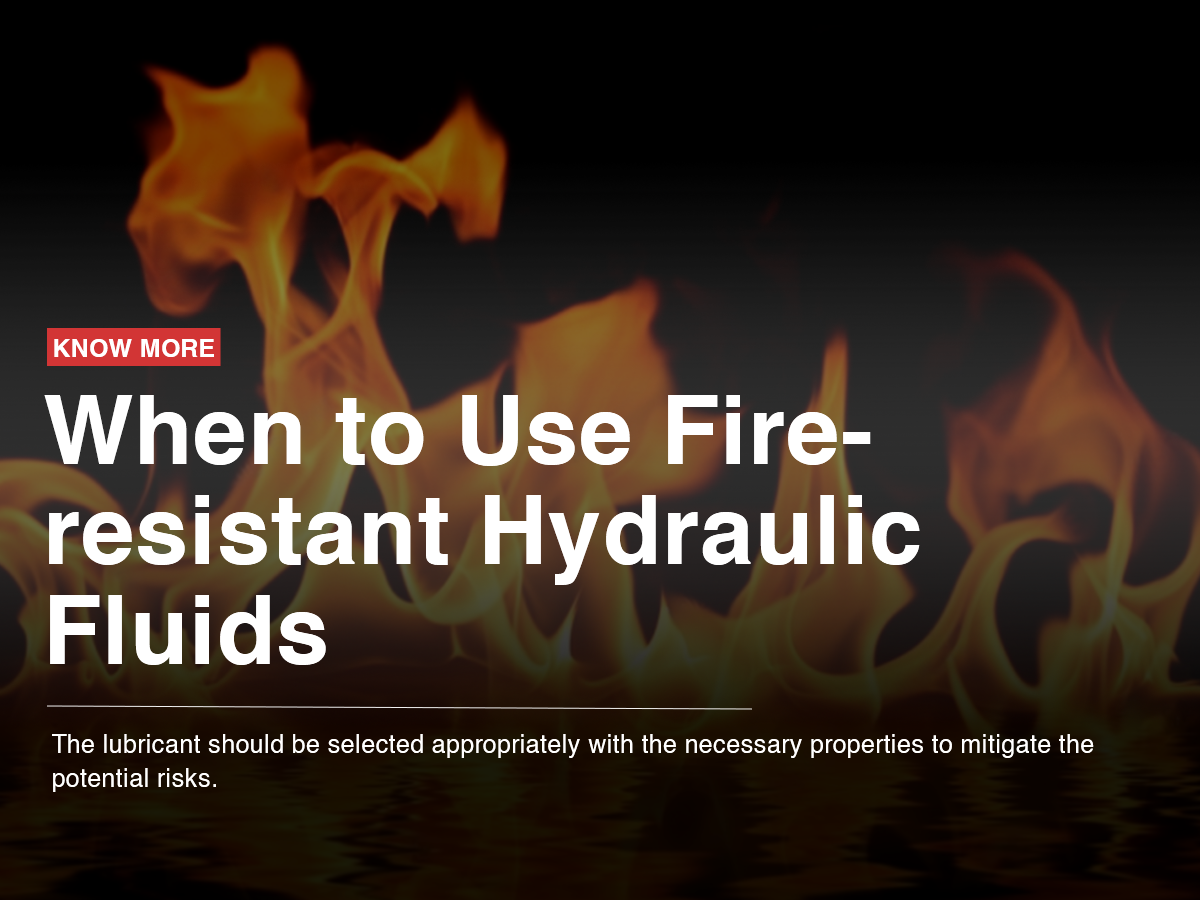
When to Use Fire-resistant Hydraulic Fluids
Selecting the appropriate lubricant with the necessary properties is essential to mitigate potential risks in hydraulic systems. When choosing lubricants, it is crucial to consider their functions, such as protecting against corrosion, wear, transferring contaminants, and dissipating heat. However, it is equally important to be mindful that certain lubricants may become flammable and can lead to hot surface conditions. The risk of fire should be especially taken into account when operating equipment with lubricated components, particularly when the lubricant used has a low flash point and is in close proximity to potential ignition sources or hot surfaces. Small leaks in pressurized lubricants can create fine sprays, increasing the susceptibility of the system to fire-related risks, especially in areas with open flames or high-temperature equipment.
Certain environments and equipment demand the use of fire-resistant fluids to ensure safety. These include die-casting machines, foundries, metalworking equipment, forging/extrusion operations, mining equipment, and power plants. The ISO 6743-4:2015 standard categorizes fire-resistant hydraulic fluids into six main types: HFAE, HFAS, HFB, HFC, HFDR, and HFDU. Each type offers different characteristics and performance benefits.
It is essential to test the flammability characteristics of industrial fluids using the FM 6930 standard and gain approvals and certifications from (FM) Factory Mutual for fire-protection equipment. Regular maintenance of water-based fire-resistant hydraulic fluids is crucial, requiring periodic testing for pH levels, corrosiveness, wear protection, controlled storage conditions, and shelf life. Consulting with lubricant manufacturers for specifications and fire-protection protocols is essential.
Contamination control is another critical aspect of maintaining hydraulic systems. Proper oil analysis is required to detect abnormal contamination levels, water concentrations, acid number fluctuations, wear debris, or changes in the properties of the lubricant. Implementing breathers with desiccants and particle filters, along with appropriate filtration and seal strategies, is essential to keep the lubricant clean, cool, and dry.
During changeovers to fire-resistant fluids, meticulous attention must be paid to cross-compatibility and residual fluid levels. Proper flushing procedures and adherence to ISO 7745 standard guidelines for changeovers are crucial to ensure successful transitions without compromising the system's integrity and performance.