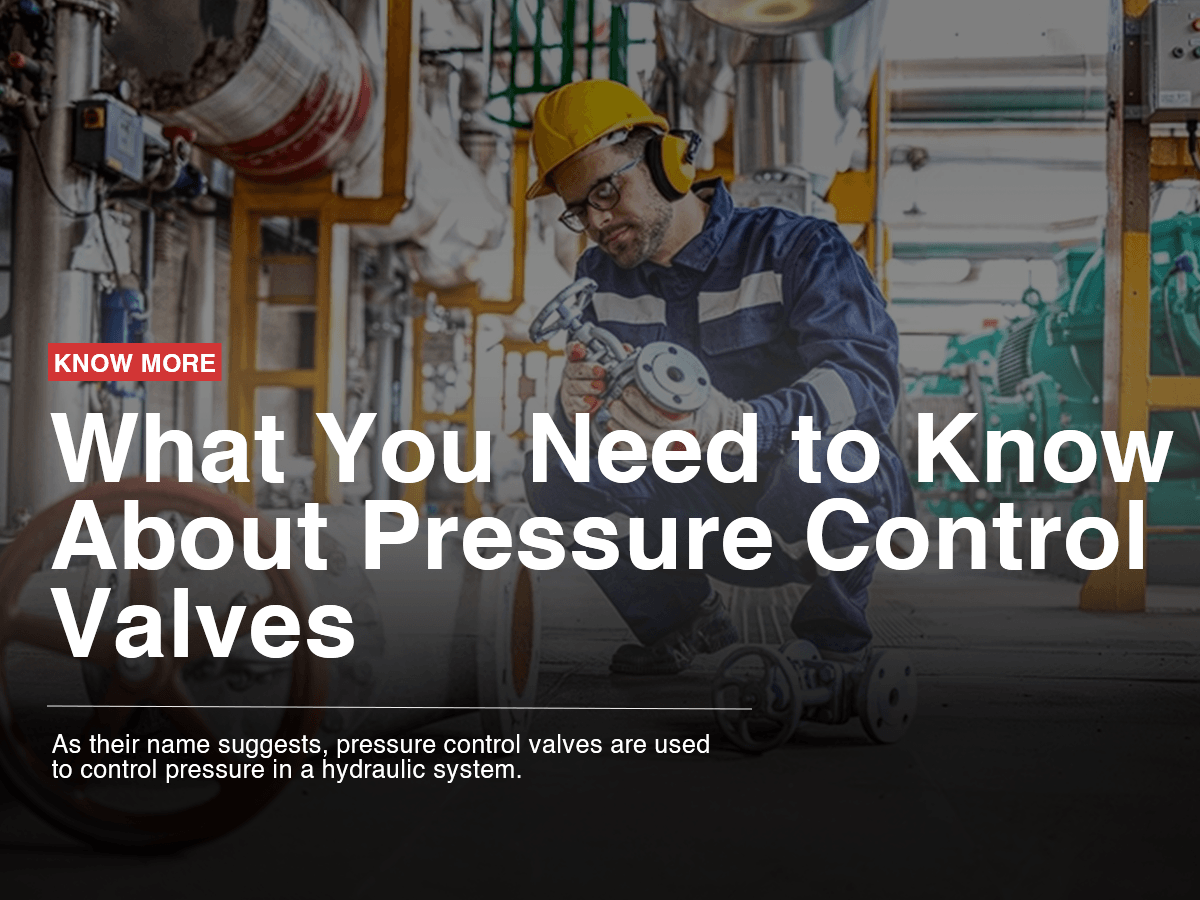
What You Need to Know About Pressure Control Valves
Pressure control valves serve the purpose of regulating pressure within a hydraulic system. They are utilized when it is necessary to maintain pressure within specific levels, as specified by the system's manufacturer or determined by the system operator.
A critical component in maintaining controlled load elevation and gradual lowering in equipment like skid steers is the counterbalance valve. This valve prevents a suspended weight from descending rapidly and allows controlled dropping. It is employed to manage movement and balance loads held in place by motors, pumps, or cylinders. Brake valves, a type of counterbalance valve, are commonly used in hydraulic drive motors of SSL or CTL equipment and hydraulic winch motors in cranes.
Pressure relief valves, also known as safety relief valves or pressure safety valves, are designed to open when the pressure reaches a specific threshold, releasing pressurized fluid from the system. This helps regulate the pressure back to the maximum specified or below, ensuring the hydraulic system's safety. The three popular pressure relief valve designs include direct-acting, direct-operated pilot type, and remote-actuated pilot type.
Reducing valves enable the flow of pressurized fluid until a predetermined pressure is achieved downstream from the valve. Once this specified pressure is reached or exceeded, the downstream pressure causes the pressure reduction valve to shut off the flow into that branch. These valves find common use in hydraulic systems requiring multiple operating system pressures and can achieve significant pressure reduction ratios.
Sequence valves, also known as hydraulic sequencing valves, operate similarly to pressure relief valves but have the added function of directing fluid to another area of the system, such as a hydraulic motor or cylinder, after reaching the preset pressure. They facilitate the organization of various actions in the hydraulic system and come in direct-acting and direct-acting pilot forms, catering to different pressure requirements.
Unloading valves are utilized to drain excess fluid into a tank under minimal or zero pressure from a pump or accumulator, typically activated by an external signal.
Understanding the fundamentals of these hydraulic valves is crucial for the proper functioning and troubleshooting of hydraulic machinery, such as hydraulic final drive motors, enabling efficient identification and resolution of potential issues within the hydraulic system.